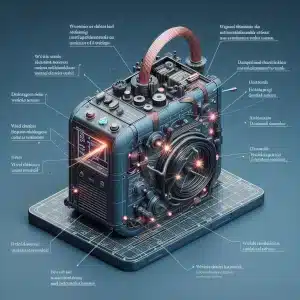
En este artículo, exploraremos en detalle las desventajas asociadas con los soldadores de hilo, centrándonos principalmente en los soldadores MIG/MAG.
Examinaremos los diversos aspectos que contribuyen a estas desventajas, desde la complejidad técnica y la sensibilidad a la contaminación hasta las limitaciones de movilidad y los desafíos al soldar materiales delgados.
Al comprender estas limitaciones, los usuarios podrán tomar decisiones más informadas al seleccionar el equipo de soldadura más adecuado para sus necesidades específicas.
En el mundo de la fabricación y la construcción, la soldadura juega un papel crucial en la unión de materiales metálicos para crear estructuras sólidas y duraderas.
Entre las múltiples técnicas de soldadura disponibles, los soldadores de hilo, especialmente los soldadores MIG/MAG, han ganado popularidad debido a su eficiencia, velocidad y versatilidad en una variedad de aplicaciones industriales.
Sin embargo, aunque los soldadores de hilo ofrecen numerosas ventajas, también presentan una serie de desventajas que deben ser consideradas por los usuarios.
Desde los costos iniciales y operativos hasta las limitaciones técnicas y medioambientales, estas desventajas pueden influir en la elección del tipo de soldador más adecuado para una tarea específica.
Los soldadores de hilo, también conocidos como soldadores MIG/MAG (Metal Inert Gas/Metal Active Gas), son herramientas muy versátiles y ampliamente utilizadas en la industria metalúrgica y de la fabricación.
Sin embargo, como cualquier otra herramienta, tienen algunas desventajas:
Costo inicial y mantenimiento
El costo inicial y el mantenimiento son consideraciones importantes al evaluar la viabilidad de utilizar soldadores MIG/MAG.
Aquí hay una ampliación de estos aspectos:
- Costo inicial elevado: Los soldadores MIG/MAG tienden a tener un costo inicial más alto en comparación con otros tipos de soldadores, como los soldadores de arco manual o los soldadores de electrodo revestido. Esto se debe a la tecnología más avanzada que utilizan, que incluye sistemas de alimentación de alambre, reguladores de gas, y controles electrónicos más sofisticados. Este costo inicial puede ser una barrera para aquellos que tienen un presupuesto limitado o que solo necesitan la soldadura ocasionalmente.
- Consumibles: Además del costo inicial del equipo, los soldadores MIG/MAG también implican costos continuos asociados con los consumibles necesarios para su funcionamiento. Estos consumibles incluyen alambres de soldadura y gases de protección. Los alambres de soldadura vienen en diferentes materiales y diámetros, y deben ser reemplazados a medida que se agotan. Del mismo modo, los gases de protección, como el argón o una mezcla de gases inertes y activos, deben ser recargados periódicamente en los tanques de gas. Estos costos adicionales deben ser considerados en el presupuesto general de soldadura.
- Mantenimiento regular: Los soldadores MIG/MAG requieren un mantenimiento regular para garantizar su funcionamiento óptimo y prolongar su vida útil. Esto incluye la limpieza y el reemplazo de componentes desgastados, como las puntas de contacto y los difusores de gas, así como la inspección y ajuste de los parámetros de soldadura. El incumplimiento del mantenimiento programado puede resultar en un rendimiento deficiente del equipo y una disminución de la calidad de la soldadura.
- Reparaciones ocasionales: A lo largo de su vida útil, es probable que los soldadores MIG/MAG requieran reparaciones ocasionales debido al desgaste normal, fallas electrónicas u otros problemas mecánicos. Estas reparaciones pueden implicar costos adicionales, tanto en términos de mano de obra como de piezas de repuesto. Además, las reparaciones pueden resultar en tiempo de inactividad del equipo, lo que podría afectar la productividad y los plazos de entrega en entornos industriales.
Aunque los soldadores MIG/MAG ofrecen ventajas significativas en términos de velocidad, eficiencia y calidad de soldadura, es importante tener en cuenta los costos iniciales y continuos asociados con su adquisición y mantenimiento.
Estos costos pueden ser una consideración importante para los usuarios que buscan equilibrar el rendimiento del equipo con su presupuesto disponible.
Consumibles
Los consumibles son una parte integral del proceso de soldadura con soldadores MIG/MAG y representan un costo continuo a largo plazo para los usuarios.
Aquí se detalla cómo los alambres de soldadura y los gases de protección contribuyen a estos costos operativos:
- Alambres de soldadura: Los soldadores MIG/MAG utilizan alambres de soldadura continuos que se alimentan automáticamente a través de un sistema de alimentación de alambre. Estos alambres están disponibles en una variedad de materiales, incluyendo acero al carbono, acero inoxidable, aluminio, y otros metales. El tipo y el diámetro del alambre de soldadura se seleccionan según el material a soldar y el grosor del metal base. A medida que se realiza la soldadura, el alambre se consume gradualmente, y eventualmente se agota, lo que requiere su reemplazo periódico. El costo de los alambres de soldadura puede variar según el material y el diámetro, y este gasto se suma a los costos operativos a largo plazo del equipo.
- Gases de protección: Los soldadores MIG/MAG utilizan gases de protección para proteger el baño de soldadura y el electrodo de la contaminación atmosférica, como el oxígeno y el nitrógeno, que podrían provocar porosidad y otras imperfecciones en la soldadura. Los gases más comúnmente utilizados son el argón, el dióxido de carbono y las mezclas de gases inertes y activos. Estos gases se suministran en cilindros o tanques y se conectan al equipo de soldadura mediante reguladores de flujo. A medida que se utiliza el soldador, el gas se consume gradualmente y eventualmente el suministro se agota, lo que requiere la recarga o el reemplazo del cilindro. El costo de los gases de protección, así como el costo de la recarga de los cilindros, contribuye significativamente a los costos operativos continuos del equipo.
En conjunto, los consumibles como los alambres de soldadura y los gases de protección representan un gasto continuo a largo plazo para los usuarios de soldadores MIG/MAG.
Estos costos deben ser considerados al calcular el costo total de propiedad del equipo y al presupuestar para proyectos de soldadura a largo plazo.
Además, la gestión eficiente de los consumibles, como la optimización de los ajustes de soldadura y la minimización del desperdicio, puede ayudar a reducir estos costos operativos y mejorar la rentabilidad del equipo.
Mantenimiento regular
El mantenimiento regular es una parte fundamental para asegurar el rendimiento óptimo y la durabilidad de los soldadores MIG/MAG.
Aquí se detalla su importancia y las tareas involucradas:
- Limpieza: Uno de los aspectos más básicos del mantenimiento es la limpieza del equipo. Durante el proceso de soldadura, pueden acumularse salpicaduras de metal fundido, polvo y residuos en diversas partes del soldador, como la boquilla de la antorcha, el rollo de alimentación de alambre y el mecanismo de alimentación. Estos residuos pueden obstruir el flujo de gas de protección o interferir con el movimiento del alambre de soldadura, lo que afecta la calidad de la soldadura. Por lo tanto, es importante limpiar regularmente todas las partes relevantes del soldador utilizando herramientas y productos adecuados.
- Reemplazo de componentes desgastados: Los soldadores MIG/MAG contienen varios componentes que experimentan desgaste durante el uso normal. Por ejemplo, las puntas de contacto, que conducen la corriente eléctrica al alambre de soldadura, se desgastan con el tiempo debido al calor y la fricción. Del mismo modo, los difusores de gas pueden obstruirse o dañarse con el tiempo, lo que afecta la distribución adecuada del gas de protección. Estos componentes deben ser inspeccionados regularmente y reemplazados según sea necesario para mantener un rendimiento óptimo del equipo.
- Inspección y ajuste de parámetros: Los soldadores MIG/MAG suelen tener varios parámetros ajustables, como la velocidad de alimentación del alambre, la corriente de soldadura y el flujo de gas de protección. Estos parámetros deben ser ajustados según las necesidades específicas de cada aplicación de soldadura. El incumplimiento en la inspección y ajuste de estos parámetros puede resultar en una soldadura de baja calidad, incluyendo falta de penetración, porosidad o irregularidades en la forma del cordón de soldadura. Por lo tanto, es crucial realizar inspecciones periódicas y ajustes de parámetros según sea necesario para garantizar resultados óptimos de soldadura.
- Calibración y mantenimiento electrónico: Además de los componentes mecánicos, los soldadores MIG/MAG también pueden tener componentes electrónicos y sistemas de control que requieren calibración y mantenimiento periódico. Esto puede incluir la verificación y ajuste de la precisión de los controles de voltaje y corriente, así como la actualización del software del equipo si es necesario. El mantenimiento electrónico adecuado es crucial para garantizar la seguridad del operador y la precisión en la entrega de energía durante el proceso de soldadura.
El mantenimiento regular de los soldadores MIG/MAG es esencial para garantizar su funcionamiento óptimo y prolongar su vida útil.
Desde la limpieza y el reemplazo de componentes desgastados hasta la inspección y ajuste de parámetros, cada tarea desempeña un papel crucial en mantener la calidad y la eficiencia de la soldadura.
El incumplimiento del mantenimiento programado puede resultar en un rendimiento deficiente del equipo y, en última instancia, en costos adicionales y una disminución en la calidad de la soldadura.
Complejidad del equipo
La complejidad del equipo es una consideración importante al utilizar soldadores MIG/MAG, ya que estos sistemas suelen ser más sofisticados en comparación con otros tipos de soldadores.
Aquí se detallan algunos aspectos que contribuyen a esta complejidad:
- Ajustes de parámetros: Los soldadores MIG/MAG ofrecen una amplia gama de ajustes de parámetros, como la velocidad de alimentación del alambre, la corriente de soldadura y el voltaje. Estos ajustes deben ser configurados correctamente para cada aplicación específica de soldadura. La velocidad de alimentación del alambre, por ejemplo, determina la cantidad de material depositado durante la soldadura, mientras que la corriente y el voltaje influyen en la penetración y la calidad del cordón de soldadura. La necesidad de ajustes precisos puede ser intimidante para usuarios principiantes que aún no tienen experiencia en la selección y configuración de estos parámetros.
- Selección de materiales y gases de protección: Los soldadores MIG/MAG permiten la soldadura de una amplia variedad de metales y aleaciones, lo que requiere la selección adecuada de materiales de relleno y gases de protección. La elección incorrecta de estos materiales puede afectar negativamente la calidad de la soldadura y la integridad estructural de la unión. Por lo tanto, los usuarios deben tener un buen entendimiento de las propiedades de los materiales y los gases de protección, así como de las especificaciones del trabajo a realizar.
- Técnica de soldadura: Además de los ajustes de parámetros, la técnica de soldadura también es un factor crucial en el proceso MIG/MAG. El ángulo de la antorcha, la velocidad de movimiento y la distancia entre el electrodo y el material de base pueden influir significativamente en la calidad y la apariencia de la soldadura. Los usuarios deben aprender y practicar técnicas adecuadas de soldadura para maximizar la eficiencia y la calidad del proceso.
- Seguridad: Debido a la naturaleza del proceso MIG/MAG, que implica el uso de altas corrientes eléctricas y gases de protección inflamables, la seguridad es una preocupación importante. Los usuarios deben estar familiarizados con las precauciones de seguridad necesarias, como el uso de equipos de protección personal, la ventilación adecuada y las prácticas seguras de manipulación y almacenamiento de gases comprimidos.
La complejidad del equipo MIG/MAG radica en la necesidad de realizar ajustes precisos de parámetros, la selección adecuada de materiales y gases de protección, el dominio de técnicas de soldadura y la atención a las consideraciones de seguridad.
Esta complejidad puede representar un desafío para usuarios principiantes que aún no han adquirido la experiencia y habilidades necesarias para operar el equipo de manera efectiva.
Sin embargo, con la capacitación adecuada y la práctica continua, los usuarios pueden superar estas dificultades y aprovechar al máximo las capacidades de los soldadores MIG/MAG.
Sensibilidad a la contaminación
La sensibilidad a la contaminación es una preocupación importante al utilizar soldadores MIG/MAG, ya que la presencia de impurezas en la superficie del material a soldar puede tener un impacto significativo en la calidad de la soldadura.
Aquí se detallan algunos aspectos relacionados con esta sensibilidad:
- Interferencia en el arco de soldadura: Durante el proceso de soldadura MIG/MAG, se genera un arco eléctrico entre el electrodo y el material base. Este arco funde el alambre de soldadura y el material base para formar la unión deseada. Sin embargo, si hay contaminantes presentes en la superficie del material base, como óxido, pintura, grasa o suciedad, pueden interferir en la formación del arco. Esto puede resultar en una soldadura de mala calidad, con defectos como porosidad, falta de fusión o inclusión de impurezas en el cordón de soldadura.
- Degradación de la protección del gas: Los soldadores MIG/MAG utilizan un gas de protección, como argón, dióxido de carbono o una mezcla de gases inertes y activos, para proteger el arco de soldadura y el cordón de soldadura de la contaminación atmosférica. Sin embargo, si la superficie del material a soldar está contaminada, los gases de protección pueden no ser efectivos para prevenir la oxidación y otras reacciones no deseadas durante la soldadura. Como resultado, la calidad de la soldadura puede verse comprometida, incluso si se utilizan parámetros de soldadura adecuados.
- Pretratamiento de superficies: Para mitigar los efectos negativos de la contaminación, es necesario realizar un pretratamiento cuidadoso de las superficies a unir antes de la soldadura. Esto puede implicar la limpieza mecánica, el lijado, el desengrasado y, en algunos casos, el uso de productos químicos para eliminar óxidos, pintura u otras impurezas superficiales. Un pretratamiento adecuado ayuda a garantizar que las superficies estén limpias y libres de contaminantes, lo que facilita la formación de un arco de soldadura estable y la obtención de una soldadura de alta calidad.
- Inspección visual y pruebas de calidad: Además del pretratamiento de superficies, es importante realizar inspecciones visuales y pruebas de calidad para verificar la integridad de la soldadura. Esto puede incluir la detección de defectos superficiales, como porosidad o inclusiones de impurezas, que pueden haber sido causados por la contaminación durante el proceso de soldadura. La detección temprana de estos defectos permite tomar medidas correctivas antes de que se conviertan en problemas más graves.
La sensibilidad a la contaminación es una consideración importante al utilizar soldadores MIG/MAG, ya que la presencia de impurezas en la superficie del material a soldar puede afectar negativamente la calidad de la soldadura.
Un pretratamiento cuidadoso de las superficies a unir, junto con inspecciones visuales y pruebas de calidad, son pasos esenciales para garantizar soldaduras de alta calidad y duraderas.
Limitaciones de movilidad
Las limitaciones de movilidad son un factor importante a considerar al utilizar soldadores MIG/MAG, ya que aunque son más portátiles que algunos otros tipos de soldadores, aún tienen ciertas restricciones que pueden dificultar su uso en ciertos entornos.
Aquí se detallan estas limitaciones:
- Necesidad de alimentación eléctrica: Los soldadores MIG/MAG requieren una fuente de alimentación eléctrica para funcionar. Aunque pueden operar con una amplia gama de voltajes de entrada y se pueden conectar a diferentes tipos de enchufes, aún dependen de la disponibilidad de energía eléctrica. Esto puede limitar su uso en ubicaciones remotas o en lugares donde no hay acceso a una fuente de alimentación eléctrica confiable. En tales situaciones, puede ser necesario utilizar generadores eléctricos o fuentes de energía alternativas, lo que agrega complejidad y costos adicionales al proceso de soldadura.
- Disponibilidad de gas de protección: Además de la alimentación eléctrica, los soldadores MIG/MAG también requieren gases de protección, como argón, dióxido de carbono o una mezcla de gases inertes y activos. Estos gases son necesarios para proteger el arco de soldadura y el cordón de soldadura de la contaminación atmosférica, asegurando una soldadura de alta calidad. Sin embargo, la disponibilidad de estos gases puede ser limitada en algunas ubicaciones remotas o en trabajos al aire libre. Esto puede hacer que sea difícil o costoso obtener los gases necesarios para el proceso de soldadura, lo que afecta la viabilidad de utilizar soldadores MIG/MAG en tales situaciones.
- Portabilidad limitada en comparación con otros tipos de soldadores: Aunque los soldadores MIG/MAG son más portátiles que algunos otros tipos de soldadores, como los soldadores de arco manual o los soldadores de electrodo revestido, aún tienen limitaciones en términos de movilidad. La necesidad de una fuente de alimentación eléctrica y la disponibilidad de gas de protección pueden restringir su uso en entornos donde la movilidad es crucial, como trabajos en altura, en andamios o en áreas de difícil acceso. En tales situaciones, los soldadores MIG/MAG pueden no ser la opción más práctica o conveniente, y puede ser necesario utilizar soldadores más portátiles y autónomos.
Aunque los soldadores MIG/MAG son más portátiles que algunos otros tipos de soldadores, aún tienen limitaciones de movilidad debido a la necesidad de alimentación eléctrica y la disponibilidad de gas de protección.
Estas limitaciones pueden hacer que sea difícil o costoso utilizarlos en ubicaciones remotas o en trabajos al aire libre donde no hay acceso a energía eléctrica confiable o gases de protección.
Es importante tener en cuenta estas limitaciones al seleccionar el tipo de soldador más adecuado para una aplicación específica.
Salpicaduras
Las salpicaduras de metal fundido son un fenómeno común en el proceso de soldadura MIG/MAG y pueden tener varias implicaciones tanto para la seguridad del operador como para la calidad de la soldadura.
Aquí se detallan los aspectos relacionados con este problema:
- Riesgos para la seguridad: Las salpicaduras de metal fundido representan un riesgo significativo para la seguridad del operador y otras personas presentes en el área de trabajo. Las pequeñas gotas de metal caliente pueden desprenderse del cordón de soldadura y proyectarse a distancias cortas, lo que puede provocar quemaduras en la piel o lesiones oculares si no se utilizan las protecciones adecuadas, como gafas de seguridad y equipos de protección personal (EPP). Además, las salpicaduras pueden causar incendios si entran en contacto con materiales inflamables cercanos.
- Impacto en la calidad de la soldadura: Las salpicaduras de metal fundido pueden afectar negativamente la calidad estética y funcional de la soldadura. Cuando las gotas de metal se adhieren a la superficie del material base o a la pieza de trabajo, pueden crear defectos visibles en el cordón de soldadura, como inclusiones o proyecciones. Estos defectos pueden comprometer la integridad estructural de la soldadura y requerir retrabajo adicional para corregirlos, lo que aumenta los costos y el tiempo de producción.
- Necesidad de limpieza adicional: Las salpicaduras de metal fundido también pueden requerir un trabajo adicional de limpieza para eliminarlas de la superficie del material base o de las piezas de trabajo. Esto puede implicar el uso de herramientas abrasivas, como cepillos de alambre o esmeriladoras, para eliminar las inclusiones de metal y restaurar la apariencia estética de la soldadura. El proceso de limpieza adicional no solo consume tiempo y recursos, sino que también puede afectar la productividad y la eficiencia del proceso de fabricación.
- Causas y prevención: Las salpicaduras de metal fundido pueden ser causadas por varios factores, incluida la presencia de impurezas en el material base, la configuración incorrecta de los parámetros de soldadura, como la velocidad de alimentación del alambre y el voltaje, y la calidad de la protección del gas. Para prevenir la formación de salpicaduras, es importante utilizar equipos de soldadura en buen estado, ajustar adecuadamente los parámetros de soldadura, limpiar y desengrasar las superficies de trabajo, y utilizar gases de protección adecuados y reguladores de flujo.
Las salpicaduras de metal fundido son un problema común en el proceso de soldadura MIG/MAG que puede tener implicaciones importantes para la seguridad del operador, la calidad de la soldadura y la eficiencia del proceso de fabricación.
Es fundamental tomar las precauciones adecuadas y seguir las mejores prácticas de soldadura para prevenir la formación de salpicaduras y minimizar sus efectos negativos.
Corrientes de aire
Las corrientes de aire representan un desafío significativo al realizar soldadura MIG/MAG, ya que pueden interferir con el arco de soldadura y afectar la calidad y la estabilidad de la soldadura.
Aquí se detallan los aspectos relacionados con este problema:
- Interferencia con el arco de soldadura: Las corrientes de aire pueden alterar la dirección y la estabilidad del arco de soldadura, lo que dificulta mantener una transferencia de metal estable y uniforme entre el electrodo y el material base. Esto puede resultar en una soldadura de calidad inferior, con defectos como porosidad, falta de fusión o inclusiones de impurezas en el cordón de soldadura. Las corrientes de aire también pueden provocar la dispersión del gas de protección, lo que aumenta el riesgo de oxidación y contaminación del cordón de soldadura.
- Problemas de protección del gas: El gas de protección utilizado en la soldadura MIG/MAG es esencial para proteger el arco de soldadura y el cordón de soldadura de la contaminación atmosférica. Sin embargo, las corrientes de aire pueden dificultar la eficacia de este gas al dispersarlo o desviar su dirección. Esto puede resultar en una protección insuficiente del arco de soldadura y la formación de defectos en la soldadura, como porosidad o inclusiones de gas.
- Dificultades en exteriores o en lugares ventilados: Debido a su sensibilidad a las corrientes de aire, la soldadura MIG/MAG puede ser más difícil de realizar en exteriores o en lugares con mucha ventilación. En estos entornos, las corrientes de aire pueden ser más fuertes y difíciles de controlar, lo que aumenta el riesgo de interferencia con el arco de soldadura y la protección del gas. Esto puede dificultar la obtención de resultados de soldadura consistentes y de alta calidad, especialmente en trabajos que requieren precisión y acabado estético.
- Medidas de control y mitigación: Para mitigar los efectos de las corrientes de aire durante la soldadura MIG/MAG, se pueden tomar varias medidas de control. Estas pueden incluir el uso de cortinas o pantallas para bloquear las corrientes de aire, la elección de ubicaciones de trabajo protegidas o el ajuste de la velocidad de alimentación del alambre y otros parámetros de soldadura para compensar los efectos de las corrientes de aire. Además, es importante realizar inspecciones visuales y pruebas de calidad para detectar y corregir cualquier defecto en la soldadura causado por la interferencia de las corrientes de aire.
Las corrientes de aire representan un desafío importante al realizar soldadura MIG/MAG, ya que pueden interferir con el arco de soldadura, la protección del gas y la calidad de la soldadura.
Es importante tomar medidas de control y mitigación para minimizar los efectos de las corrientes de aire y garantizar resultados de soldadura consistentes y de alta calidad, especialmente en entornos exteriores o con mucha ventilación.
Acceso
El acceso limitado es un desafío significativo al utilizar soldadura MIG/MAG, especialmente en áreas donde el equipo puede ser difícil de maniobrar o donde el espacio es restringido.
Aquí se detallan varios aspectos relacionados con este desafío:
- Tamaño y peso del equipo: Los soldadores MIG/MAG, junto con sus accesorios y suministros adicionales, pueden ser relativamente grandes y pesados. Esto puede dificultar su transporte y manipulación en áreas con acceso limitado, como espacios reducidos dentro de estructuras o áreas confinadas. Además, el equipo puede requerir una superficie estable y plana para su operación, lo que puede limitar aún más su uso en terrenos irregulares o en áreas congestionadas.
- Dificultades para maniobrar en áreas estrechas: El tamaño y la forma del equipo, incluida la antorcha de soldadura y los cables de alimentación, pueden dificultar su uso en áreas estrechas o de difícil acceso. Esto puede ser especialmente problemático al soldar piezas de trabajo con geometrías complejas o en espacios confinados donde no hay suficiente espacio para maniobrar el equipo de soldadura de manera eficiente.
- Acceso a puntos de soldadura difíciles: En algunas aplicaciones, puede ser necesario soldar en áreas de difícil acceso, como juntas estrechas, ángulos agudos o áreas con restricciones de visibilidad. Esto puede requerir el uso de técnicas especiales de soldadura, así como la modificación o adaptación del equipo para permitir el acceso adecuado a estos puntos de soldadura. En algunos casos, puede ser necesario utilizar antorchas de soldadura especiales o accesorios de extensión para alcanzar estos puntos de manera efectiva.
- Riesgo de daños al equipo y a las piezas de trabajo: El uso de la soldadura MIG/MAG en áreas de difícil acceso también puede aumentar el riesgo de daños tanto al equipo de soldadura como a las piezas de trabajo. La manipulación y la instalación del equipo en espacios estrechos pueden resultar en colisiones con objetos cercanos o en daños accidentales a las piezas de trabajo durante el proceso de soldadura. Esto resalta la importancia de tener cuidado y planificar con anticipación para minimizar el riesgo de daños.
El acceso limitado puede presentar desafíos significativos al utilizar soldadura MIG/MAG, especialmente en áreas donde el equipo puede ser difícil de maniobrar o donde el espacio es restringido.
Es importante considerar estos desafíos al planificar y ejecutar proyectos de soldadura en entornos con acceso limitado, y adoptar medidas apropiadas para garantizar la seguridad, la eficiencia y la calidad del proceso de soldadura.
Materiales delgados
Soldar materiales delgados con soldadura MIG/MAG puede presentar desafíos debido a la alta energía térmica generada por este proceso.
Aquí se detallan los factores que contribuyen a esta limitación:
- Exceso de calor: La soldadura MIG/MAG involucra la transferencia de grandes cantidades de calor al área de trabajo. En materiales delgados, este exceso de calor puede resultar en una rápida acumulación de temperatura, lo que aumenta el riesgo de deformaciones, distorsiones y quemaduras a través del material. El material delgado tiene una capacidad limitada para disipar el calor, lo que puede provocar que se vuelva extremadamente caliente y se deforme fácilmente.
- Fusión excesiva: Los materiales delgados son más susceptibles a la fusión excesiva durante la soldadura MIG/MAG. La alta corriente eléctrica utilizada en este proceso puede causar que el material se funda más allá de lo necesario, resultando en orificios, perforaciones o debilitamiento estructural en el material base. Esta fusión excesiva puede comprometer la integridad de la soldadura y conducir a fallas prematuras en la pieza soldada.
- Control de la penetración: La soldadura MIG/MAG puede tener dificultades para controlar la penetración en materiales delgados. Debido a la alta energía térmica involucrada, es difícil lograr una soldadura de penetración superficial en materiales delgados sin dañar el material subyacente. Esto puede resultar en una soldadura deficiente que no proporciona una unión sólida y duradera entre las piezas.
- Técnicas de soldadura especiales: Soldar materiales delgados con soldadura MIG/MAG requiere el uso de técnicas especiales para minimizar el calor aplicado y controlar la penetración. Esto puede incluir la reducción de la corriente de soldadura, el uso de alambres de menor diámetro, la disminución de la velocidad de avance y la implementación de técnicas de soldadura pulsada para controlar la transferencia de calor. Sin embargo, incluso con estas técnicas, todavía puede ser difícil evitar completamente las deformaciones en materiales extremadamente delgados.
Aunque la soldadura MIG/MAG es adecuada para una amplia variedad de aplicaciones, puede no ser la mejor opción para soldar materiales extremadamente delgados debido al exceso de calor y la dificultad para controlar la penetración.
En tales casos, puede ser preferible utilizar procesos de soldadura de menor energía térmica, como la soldadura por puntos, la soldadura por resistencia o la soldadura TIG, que ofrecen una mayor precisión y control en la soldadura de materiales delgados.
Curva de aprendizaje
La curva de aprendizaje en la soldadura MIG/MAG es un aspecto importante a considerar, ya que aunque la técnica en sí misma puede ser relativamente sencilla de entender, dominarla y obtener resultados óptimos requiere tiempo, práctica y experiencia.
Aquí se detallan los elementos que contribuyen a esta curva de aprendizaje:
- Conocimiento técnico: Para soldar eficazmente con MIG/MAG, los operadores deben comprender los principios básicos de la soldadura, incluyendo la transferencia de calor, la fusión del material de relleno y el metal base, y la formación del cordón de soldadura. Además, es importante comprender cómo ajustar y controlar los parámetros de soldadura, como la velocidad de alimentación del alambre, el voltaje y la corriente, para adaptarse a diferentes materiales y espesores.
- Habilidad práctica: La soldadura MIG/MAG requiere habilidades prácticas específicas, como la manipulación adecuada de la antorcha de soldadura, la técnica de alimentación del alambre y el control del arco de soldadura. Esto incluye mantener una distancia y ángulo consistentes entre la antorcha y el material, así como moverse suavemente a lo largo de la junta de soldadura para asegurar una distribución uniforme del material de relleno.
- Comprensión de la metalurgia: Para obtener resultados óptimos, los soldadores MIG/MAG deben tener una comprensión básica de la metalurgia y cómo diferentes metales y aleaciones responden al calor y al proceso de soldadura. Esto les permite seleccionar el material de relleno adecuado, ajustar los parámetros de soldadura para adaptarse a las propiedades del material base y prevenir problemas como la porosidad, la falta de fusión o la fragilización por el calor.
- Resolución de problemas: A medida que los operadores adquieren experiencia, también desarrollan habilidades para identificar y resolver problemas comunes de soldadura, como las salpicaduras, las inclusiones de escoria y las irregularidades en el cordón de soldadura. Esto puede implicar ajustar los parámetros de soldadura, limpiar y preparar adecuadamente las superficies de trabajo, o cambiar la técnica de soldadura según sea necesario para mejorar la calidad de la soldadura.
- Práctica continua: Como con cualquier habilidad, la práctica continua es fundamental para mejorar y mantener la destreza en la soldadura MIG/MAG. Esto puede implicar la participación en programas de capacitación y certificación, la realización de proyectos de soldadura práctica y la colaboración con otros soldadores más experimentados para compartir conocimientos y técnicas.
Aunque la técnica de soldadura MIG/MAG puede ser relativamente sencilla de entender, alcanzar un nivel de habilidad y experiencia para obtener resultados óptimos requiere tiempo, práctica y dedicación.
La curva de aprendizaje puede variar según la habilidad natural del individuo, la disponibilidad de recursos de capacitación y la exposición a una variedad de aplicaciones de soldadura.
Sin embargo, con la práctica continua y el compromiso con la mejora, los operadores pueden alcanzar un alto nivel de habilidad en la soldadura MIG/MAG y lograr resultados de alta calidad en sus trabajos de soldadura.
Conclusiones sobre las desventajas de los soldadores de hilo
Las desventajas de los soldadores de hilo, como los soldadores MIG/MAG, abarcan una variedad de aspectos que van desde costos operativos hasta limitaciones técnicas.
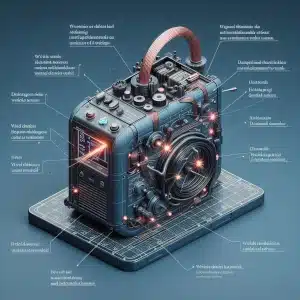
Aquí hay algunas conclusiones sobre estas desventajas:
- Costo inicial y operativo: Los soldadores MIG/MAG suelen tener un costo inicial más elevado en comparación con otros tipos de soldadores, lo que puede representar una barrera de entrada para algunos usuarios. Además, los costos operativos continuos, como los consumibles (alambres de soldadura y gases de protección) y el mantenimiento regular, pueden aumentar los gastos a lo largo del tiempo.
- Complejidad técnica: La operación de los soldadores MIG/MAG puede resultar más compleja, especialmente para usuarios principiantes, debido a la necesidad de ajustar con precisión parámetros como la velocidad de alimentación del alambre, la corriente y el voltaje. Esto requiere práctica y experiencia para obtener resultados óptimos y consistentes.
- Sensibilidad a la contaminación y a las corrientes de aire: Los soldadores MIG/MAG son sensibles a la contaminación en la superficie del material a soldar y a las corrientes de aire, lo que puede afectar negativamente la calidad de la soldadura. Esto puede requerir un pretratamiento cuidadoso de las superficies a unir y limitar su uso en exteriores o en lugares con mucha ventilación.
- Limitaciones de movilidad y acceso: Aunque son más portátiles que algunos otros tipos de soldadores, los soldadores MIG/MAG aún están limitados por la necesidad de alimentación eléctrica y la disponibilidad de gas de protección. Esto puede dificultar su uso en ubicaciones remotas o en zonas de difícil acceso, lo que puede afectar la eficiencia y la versatilidad del proceso de soldadura.
- Desafíos al soldar materiales delgados: Los soldadores MIG/MAG pueden no ser la mejor opción para soldar materiales delgados debido al exceso de calor generado durante el proceso, lo que puede causar deformaciones y dificultar el control de la penetración. Esto puede requerir técnicas especiales y experiencia adicional para lograr resultados óptimos.
En general, aunque los soldadores de hilo ofrecen muchas ventajas en términos de velocidad y eficiencia de soldadura, es importante tener en cuenta estas desventajas al seleccionar el tipo de soldador más adecuado para una aplicación específica.
Un análisis cuidadoso de los requisitos del trabajo y las limitaciones del equipo puede ayudar a minimizar los impactos negativos y optimizar los resultados de la soldadura.
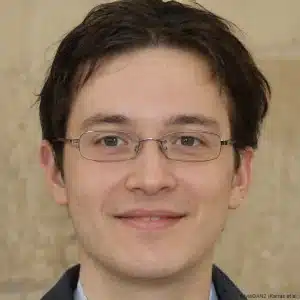
Con más de 25 años de experiencia en el sector de las ventas de equipamiento para el hogar, herramientas de bricolaje, y en los últimos 15 años en una empresa de reformas de albañilería, venta de azulejos y materiales de construcción, estufas leña, pellets, chimeneas, sistemas de calefacción.
Máster Técnico Superior en riesgos laborales.
Licenciado por la Universidad de Alicante ua.es