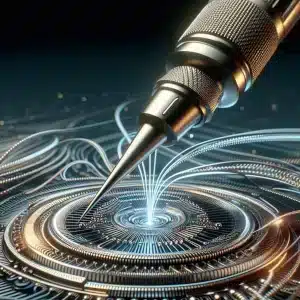
Para soldar materiales delgados, lo ideal es usar polaridad inversa. En este caso, el electrodo se conecta al polo positivo (+) de la soldadora y la pinza de masa al polo negativo (-).
En la soldadura de materiales delgados, como láminas metálicas finas o tubos delgados, es crucial controlar cuidadosamente la cantidad de calor aplicado para evitar la deformación excesiva o el agrietamiento.
La polaridad inversa, también conocida como electrodo positivo (EP) o corriente directa con el electrodo en el polo positivo (+), es a menudo preferida en este contexto.
Aquí hay una explicación más detallada de por qué la polaridad inversa es ideal para soldar materiales delgados:
Polaridad soldar materiales delgados en función del tipo de soldadura
La polaridad de soldadura para materiales delgados puede depender del tipo de soldadura que estés realizando. Aquí hay algunas pautas generales:
Soldadura por arco con electrodo revestido (SMAW o «stick»)
La soldadura por arco con electrodo revestido (SMAW o «stick») es un proceso comúnmente utilizado en una variedad de aplicaciones, incluyendo la soldadura de materiales delgados.
Aquí se desarrolla por qué se prefiere utilizar la polaridad de corriente continua (DC) con el electrodo en el polo positivo (+) para soldar materiales delgados en el proceso SMAW:
- Reducción de la penetración excesiva: La polaridad de corriente continua con el electrodo en el polo positivo (+) ayuda a reducir la penetración excesiva del material base durante el proceso de soldadura. En este caso, los electrones fluyen desde el electrodo hacia el material base, lo que calienta principalmente la pieza de trabajo en lugar del electrodo. Esta configuración resulta en una menor penetración de la soldadura en el material base, lo que es deseable al soldar materiales delgados para evitar perforaciones o deformaciones no deseadas.
- Minimización de la deformación: Al utilizar la polaridad de corriente continua con el electrodo en el polo positivo (+), se minimiza la cantidad de calor que se introduce en el material base. Esto ayuda a reducir la distorsión térmica y la deformación del material delgado durante el proceso de soldadura. Con menos calor aplicado al material, se reduce la probabilidad de que se produzcan deformaciones no deseadas, lo que contribuye a mantener la integridad estructural y la forma original del material delgado.
- Control del arco: La polaridad de corriente continua con el electrodo en el polo positivo (+) también proporciona un mejor control del arco durante el proceso de soldadura. Esto permite al soldador ajustar la longitud del arco y la velocidad de avance del electrodo con mayor precisión, lo que es especialmente importante al soldar materiales delgados que requieren un control cuidadoso para evitar daños en el material.
- Menor riesgo de contaminación: Al utilizar la polaridad de corriente continua con el electrodo en el polo positivo (+), se reduce el riesgo de contaminación del material base con elementos del revestimiento del electrodo. Esto puede ser un problema en la polaridad inversa, donde el electrodo actúa como el cátodo y puede generar más escoria y salpicaduras, que pueden contaminar la soldadura.
Al soldar materiales delgados con el proceso SMAW, se prefiere utilizar la polaridad de corriente continua con el electrodo en el polo positivo (+) debido a su capacidad para reducir la penetración excesiva, minimizar la deformación, proporcionar un mejor control del arco y reducir el riesgo de contaminación.
Estas características son fundamentales para lograr soldaduras de alta calidad en materiales delgados, manteniendo su integridad estructural y evitando deformaciones no deseadas.
Soldadura MIG/MAG (GMAW o FCAW)
En la soldadura MIG/MAG (Gas Metal Arc Welding o GMAW, y Metal Active Gas Welding o MAG), la elección de la polaridad es un factor crucial que afecta la calidad y la eficacia de la soldadura.
La polaridad inversa es la configuración más comúnmente utilizada en este proceso, especialmente al soldar materiales delgados.
Aquí se desarrolla por qué se prefiere utilizar la polaridad inversa en la soldadura MIG/MAG para materiales delgados:
- Mejora de la transferencia de metal de relleno: En la polaridad inversa, donde el electrodo es negativo (-) y la pieza de trabajo es positiva (+), se produce una transferencia más controlada y dirigida del metal de relleno desde el electrodo hacia la pieza de trabajo. Esto se debe a que los electrones fluyen desde el electrodo hacia la pieza de trabajo, lo que proporciona una fuerza adicional que ayuda a impulsar el metal de relleno hacia la junta de soldadura de manera más precisa y uniforme. Esta transferencia de metal de relleno mejorada es particularmente beneficiosa al soldar materiales delgados, donde se requiere una mayor precisión para evitar agujeros, penetración excesiva o irregularidades en la soldadura.
- Estabilidad del arco: La polaridad inversa también contribuye a un arco de soldadura más estable en la soldadura MIG/MAG. Con el electrodo conectado al polo negativo (-), se genera un arco más controlado y direccional, lo que facilita el control preciso del proceso de soldadura. Esta estabilidad del arco es crucial al trabajar con materiales delgados, donde se necesita un arco suave y estable para evitar la distorsión del material y lograr una soldadura uniforme y de alta calidad.
- Reducción del riesgo de deformación térmica: Al utilizar la polaridad inversa en la soldadura MIG/MAG, se introduce menos calor en el material base, lo que ayuda a reducir el riesgo de deformación térmica. Esto es particularmente importante al soldar materiales delgados, ya que son más susceptibles a la deformación debido a los cambios en la temperatura. Al minimizar la cantidad de calor aplicado al material base, se reduce la probabilidad de que se produzcan deformaciones no deseadas durante el proceso de soldadura.
La polaridad inversa en la soldadura MIG/MAG ofrece una mejor transferencia de metal de relleno, una mayor estabilidad del arco y una reducción del riesgo de deformación térmica, lo que la hace altamente beneficiosa para soldar materiales delgados.
Esta configuración proporciona las condiciones ideales para lograr soldaduras de alta calidad en materiales delgados, garantizando una unión sólida y duradera sin comprometer la integridad del material.
Soldadura TIG (GTAW)
En la soldadura TIG (Gas Tungsten Arc Welding o GTAW), la elección entre corriente continua (DC) o corriente alterna (AC) depende del tipo de material y del proceso específico de soldadura.
Para materiales delgados, como láminas metálicas finas o tubos delgados, se prefiere comúnmente utilizar corriente continua con electrodo positivo (DC+).
A continuación, se desarrolla por qué esta configuración puede ser preferible para soldar materiales delgados en el proceso de soldadura TIG:
- Penetración más baja: La corriente continua con electrodo positivo (DC+) tiende a producir una penetración de soldadura más baja en comparación con otras configuraciones de corriente, como DC negativo o corriente alterna. Esto significa que el calor generado durante la soldadura se concentra más en la superficie del material base y produce una penetración menos profunda. Para materiales delgados, donde se busca evitar la penetración excesiva que pueda causar agujeros o perforaciones en el material, una penetración más baja es preferible.
- Arco más estable: La corriente continua con electrodo positivo (DC+) también puede proporcionar un arco de soldadura más estable en comparación con otras configuraciones de corriente. El electrodo positivo actúa como el cátodo, lo que permite una transferencia de calor más controlada y una dirección más precisa del arco. Esto resulta en un arco más suave y estable, lo que facilita el control del proceso de soldadura, especialmente al trabajar con materiales delgados que requieren precisión y atención a los detalles.
- Menor riesgo de deformación: Al utilizar corriente continua con electrodo positivo (DC+), se introduce menos calor en el material base en comparación con otras configuraciones de corriente. Esto ayuda a reducir el riesgo de deformación térmica en materiales delgados, donde la distorsión del material debido al calor puede ser un problema. Al minimizar la cantidad de calor aplicado al material base, se reduce la probabilidad de que se produzcan deformaciones no deseadas durante el proceso de soldadura.
La corriente continua con electrodo positivo (DC+) en la soldadura TIG ofrece una penetración más baja, un arco más estable y un menor riesgo de deformación térmica, lo que la hace preferible para soldar materiales delgados.
Esta configuración proporciona las condiciones ideales para lograr soldaduras de alta calidad en materiales delgados, manteniendo su integridad estructural y evitando deformaciones no deseadas.
Menor penetración
La penetración de la soldadura se refiere a la profundidad hasta la cual el metal de soldadura se funde y se une con el material base.
En el proceso de soldadura, es crucial controlar la penetración para evitar problemas como agujeros o perforaciones en materiales delgados, ya que esto comprometería su integridad estructural.
Cuando se utiliza la polaridad inversa en la soldadura, con el electrodo conectado al polo positivo (+) de la fuente de energía y la pinza de masa al polo negativo (-), se produce una distribución de calor diferente en comparación con la polaridad directa.
En la polaridad inversa, la mayor parte del calor se concentra en el electrodo, lo que resulta en una menor penetración en el material base.
Esta menor penetración es beneficiosa para materiales delgados por varias razones:
- Evita la perforación del material: Los materiales delgados son más susceptibles a la perforación durante el proceso de soldadura si la penetración es excesiva. Esto puede ocurrir fácilmente con la polaridad directa, donde el calor puede penetrar demasiado en el material base, perforándolo y comprometiendo su integridad.
- Minimiza la deformación: La menor penetración reduce la cantidad de calor que se introduce en el material base. Esto ayuda a minimizar la deformación térmica, que es una preocupación importante al soldar materiales delgados. La deformación térmica puede causar distorsión en la forma del material, lo que afecta su funcionalidad y apariencia.
- Control de la soldadura: Con una penetración reducida, es más fácil controlar el proceso de soldadura, especialmente en aplicaciones que requieren precisión y atención a los detalles. Esto permite al soldador ajustar la técnica y la velocidad de avance para lograr una unión sólida sin comprometer la integridad del material base.
Al utilizar la polaridad inversa en la soldadura de materiales delgados, se logra una penetración reducida que ayuda a prevenir la perforación del material, minimiza la deformación térmica y permite un mayor control del proceso de soldadura.
Esto garantiza una unión sólida y duradera sin comprometer la integridad estructural del material delgado.
Control de calor
El control preciso del calor es esencial en la soldadura de materiales delgados para evitar la deformación y la distorsión del material base.
La polaridad inversa, donde el electrodo está conectado al polo positivo (+) de la fuente de energía y la pinza de masa al polo negativo (-), ofrece ventajas significativas en términos de control del calor, especialmente en materiales delgados.
Aquí se desarrolla cómo la polaridad inversa contribuye a este control:
- Menor penetración de calor: Como se mencionó anteriormente, la polaridad inversa tiende a producir una penetración de soldadura más baja en comparación con la polaridad directa. Esto significa que menos calor se transfiere al material base durante el proceso de soldadura. Con menos calor introducido en el material, se reduce el riesgo de sobrecalentamiento y deformación.
- Distribución más uniforme del calor: Debido a la menor penetración de calor, la distribución del calor en el material base tiende a ser más uniforme con la polaridad inversa. Esto es crucial para evitar puntos calientes que podrían causar distorsión localizada o deformación en el material delgado.
- Control de la velocidad de avance: Con la polaridad inversa y su menor penetración de calor, los soldadores tienen más flexibilidad para controlar la velocidad de avance del electrodo. Una velocidad de avance más lenta permite una exposición más controlada al calor y ayuda a mantener el material a una temperatura más uniforme, lo que minimiza la deformación.
- Reducción del riesgo de quemaduras: La polaridad inversa también puede ayudar a reducir el riesgo de quemar el material base. Dado que menos calor se transfiere al material, es menos probable que se produzcan quemaduras o daños superficiales, lo que es especialmente importante en materiales delgados que son más sensibles al calor.
Al utilizar la polaridad inversa en la soldadura de materiales delgados, se logra un control más preciso del calor. Esto se traduce en una distribución más uniforme del calor, una menor penetración de calor en el material base y, en última instancia, una reducción del riesgo de deformación y distorsión.
Este control del calor es esencial para mantener la forma y la integridad del material delgado durante el proceso de soldadura.
Arco más estable
El arco de soldadura es una parte crucial del proceso de soldadura, ya que proporciona la energía necesaria para fundir el electrodo y el material base, creando así una unión sólida.
La estabilidad del arco es fundamental para garantizar una soldadura de alta calidad, especialmente al trabajar con materiales delgados que son más sensibles a los cambios en el proceso de soldadura.
Aquí se desarrolla cómo la polaridad inversa contribuye a la estabilidad del arco y por qué es crucial al soldar materiales delgados:
- Menor salpicadura: Con la polaridad inversa, se puede lograr una transferencia de metal de relleno más suave y controlada, lo que reduce la cantidad de salpicadura que puede ocurrir durante el proceso de soldadura. La salpicadura excesiva puede ser problemática al soldar materiales delgados, ya que puede causar daños en el material base o requerir trabajo adicional para eliminarla, lo que puede afectar la calidad de la soldadura.
- Arco más concentrado: La polaridad inversa tiende a concentrar el arco de soldadura en el electrodo, lo que resulta en un arco más focalizado y estable. Esta mayor concentración de energía en el electrodo facilita un control más preciso del arco durante el proceso de soldadura. Al soldar materiales delgados, donde la precisión es fundamental, un arco más estable permite al soldador mantener un control cuidadoso sobre la zona de soldadura para evitar daños en el material.
- Reducción de la deformación: Un arco de soldadura más estable también puede ayudar a reducir la deformación térmica en materiales delgados. Al mantener un arco uniforme y estable, se minimiza la cantidad de calor introducido en el material base, lo que a su vez reduce el riesgo de deformación y distorsión del material durante el proceso de soldadura.
- Facilita la maniobrabilidad: Al soldar materiales delgados, es crucial poder maniobrar el electrodo con precisión para evitar daños en el material. Un arco de soldadura más estable facilita esta maniobrabilidad, permitiendo al soldador mantener un control constante sobre la dirección y la velocidad de avance del electrodo para obtener resultados óptimos.
La polaridad inversa puede proporcionar un arco de soldadura más estable, lo que facilita el control del proceso de soldadura, especialmente al trabajar con materiales delgados.
Un arco más estable ayuda a reducir la salpicadura, concentrar la energía en el electrodo, minimizar la deformación y facilitar la maniobrabilidad, lo que contribuye a una soldadura de alta calidad y a la preservación de la integridad del material delgado.
Menor riesgo de quemaduras
Cuando se trabaja con materiales delgados en el proceso de soldadura, existe un riesgo significativo de quemar el material debido al exceso de calor.
Este riesgo puede ser mitigado utilizando la polaridad inversa, donde el electrodo está conectado al polo positivo (+) de la fuente de energía y la pinza de masa al polo negativo (-).
A continuación, se desarrolla cómo la polaridad inversa ayuda a reducir el riesgo de quemaduras en materiales delgados durante el proceso de soldadura:
- Concentración del calor en el electrodo: En la polaridad inversa, la mayor parte del calor se concentra en el electrodo en lugar del material base. Esto se debe a que los electrones fluyen desde el electrodo hacia el material base, lo que genera una mayor energía y temperatura en el electrodo. Como resultado, el calor aplicado al material base es menos intenso en comparación con la polaridad directa, donde el calor se concentra más en el material base.
- Menor transferencia de calor al material base: La concentración del calor en el electrodo significa que se transfiere menos calor al material base durante el proceso de soldadura. Esto es crucial para materiales delgados, que son más sensibles al calor y tienen una menor capacidad para disiparlo. Al reducir la cantidad de calor que se transfiere al material base, se disminuye el riesgo de sobrecalentamiento y quemaduras en el material, lo que ayuda a preservar su integridad y calidad.
- Control de la velocidad de avance: Con la polaridad inversa, los soldadores tienen la flexibilidad de ajustar la velocidad de avance del electrodo para controlar aún más el calor aplicado al material base. Una velocidad de avance más lenta permite una exposición más controlada al calor, lo que ayuda a evitar que el material se caliente demasiado y se queme.
- Reducción de la deformación térmica: Al reducir el riesgo de quemaduras en el material delgado, también se minimiza la deformación térmica. La deformación térmica ocurre cuando el material se calienta de manera desigual y se expande de forma no uniforme. Al mantener el calor aplicado al mínimo necesario, se reduce la posibilidad de deformación térmica, lo que contribuye a mantener la forma y la integridad del material delgado.
Al utilizar la polaridad inversa en la soldadura de materiales delgados, se concentra el calor en el electrodo, lo que reduce el riesgo de quemaduras en el material base.
Esta concentración de calor, junto con el control de la velocidad de avance y la reducción de la deformación térmica, ayuda a preservar la integridad y calidad del material delgado durante el proceso de soldadura.
Menor distorsión
La distorsión del material durante el proceso de soldadura es un fenómeno común que puede ocurrir debido a la aplicación de calor y la contracción térmica del metal.
Cuando se trabaja con materiales delgados, la distorsión puede ser aún más pronunciada debido a la sensibilidad del material a los cambios de temperatura.
Aquí se desarrolla cómo la soldadura con polaridad inversa contribuye a minimizar la distorsión del material:
- Menor penetración de calor: La polaridad inversa tiende a producir una penetración de soldadura más baja en comparación con la polaridad directa. Esto significa que se introduce menos calor en el material base durante el proceso de soldadura. Con menos calor, hay menos riesgo de sobrecalentamiento y, por lo tanto, menos distorsión del material.
- Control del calor más preciso: Con la polaridad inversa, es posible controlar el calor aplicado al material base de manera más precisa. Esto se debe a que la mayor parte del calor se concentra en el electrodo, lo que permite al soldador ajustar la velocidad de avance y la técnica de soldadura para mantener la temperatura del material base dentro de límites aceptables. Al tener un mayor control sobre el calor, se puede minimizar la distorsión del material.
- Distribución más uniforme del calor: La polaridad inversa también puede contribuir a una distribución más uniforme del calor en el material base. Al concentrar el calor en el electrodo y minimizar la penetración en el material base, se reduce la posibilidad de que se formen gradientes de temperatura significativos dentro del material. Una distribución más uniforme del calor ayuda a prevenir la deformación localizada y la distorsión del material.
- Menor contracción térmica: La contracción térmica es un factor importante que contribuye a la distorsión del material durante la soldadura. Al minimizar la cantidad de calor introducido en el material base, se reduce la contracción térmica asociada. Esto ayuda a mantener la forma original del material y reduce la probabilidad de que se produzca distorsión durante el proceso de soldadura.
La soldadura con polaridad inversa ayuda a minimizar la distorsión del material durante el proceso de soldadura mediante la reducción de la penetración de calor, el control preciso del calor, la distribución más uniforme del calor y la reducción de la contracción térmica.
Esto es especialmente importante al trabajar con materiales delgados, donde la distorsión puede tener un impacto significativo en la integridad y la calidad del producto final.
Ventajas de la polaridad inversa para materiales delgados
La polaridad inversa, donde el electrodo se conecta al polo negativo (-) y la pieza de trabajo al polo positivo (+), ofrece varias ventajas significativas al soldar materiales delgados.
Aquí se desarrollan algunas de las principales ventajas de utilizar la polaridad inversa para materiales delgados:
- Menor penetración de calor: En la polaridad inversa, la mayor parte del calor se concentra en el electrodo, lo que resulta en una menor penetración de calor en el material base. Esto es especialmente beneficioso al soldar materiales delgados, donde la penetración excesiva puede causar agujeros, perforaciones o deformaciones no deseadas en el material. La menor penetración de calor ayuda a controlar la cantidad de calor aplicado al material, lo que reduce el riesgo de dañarlo durante el proceso de soldadura.
- Reducción del riesgo de distorsión: Al introducir menos calor en el material base, la polaridad inversa ayuda a minimizar la deformación térmica y la distorsión del material delgado durante el proceso de soldadura. Esto es crucial para mantener la forma y la integridad del material, especialmente en aplicaciones donde se requiere una alta precisión y estabilidad dimensional.
- Mejora del control del arco: La polaridad inversa proporciona un arco de soldadura más estable y controlado, lo que facilita el control preciso del proceso de soldadura. Un arco más estable es especialmente importante al soldar materiales delgados, donde se requiere un control fino para evitar daños en el material. La polaridad inversa permite al soldador ajustar la longitud del arco y la velocidad de avance del electrodo con mayor precisión, lo que contribuye a una soldadura más uniforme y de alta calidad.
- Reducción de la salpicadura y la contaminación: La polaridad inversa puede ayudar a reducir la cantidad de salpicaduras y la contaminación del material base durante el proceso de soldadura. Al concentrar el calor en el electrodo, se minimiza la formación de escoria y salpicaduras, lo que ayuda a mantener una soldadura más limpia y libre de defectos. Esto es especialmente importante al soldar materiales delgados, donde incluso pequeñas cantidades de escoria o salpicaduras pueden afectar negativamente la calidad de la soldadura.
La polaridad inversa ofrece varias ventajas para soldar materiales delgados, incluida una menor penetración de calor, una reducción del riesgo de distorsión, un mejor control del arco y una reducción de la salpicadura y la contaminación.
Estas ventajas contribuyen a la obtención de soldaduras de alta calidad en materiales delgados, manteniendo su integridad y asegurando un rendimiento óptimo en diversas aplicaciones.
Electrodos recomendados para soldar materiales delgados con polaridad inversa
Los materiales delgados requieren un enfoque cuidadoso durante el proceso de soldadura para evitar la penetración excesiva, la distorsión y otros problemas relacionados con el calor.
La elección del electrodo adecuado es crucial para lograr soldaduras de alta calidad en estos materiales. Aquí se desarrollan los tres tipos de electrodos recomendados para soldar materiales delgados con polaridad inversa:
- E6013:
- Tipo: Electrodo celulósico con bajo contenido de hidrógeno.
- Características: Este electrodo produce un arco suave y estable, lo que lo hace adecuado para soldar materiales delgados donde se requiere un control preciso del calor. La buena penetración del arco es importante para garantizar una fusión adecuada del metal de relleno con el material base sin comprometer su integridad.
- Aplicaciones: Se utiliza comúnmente en la soldadura de acero al carbono y estructuras ligeras, donde se requiere una alta maniobrabilidad y un arco controlado para evitar la deformación del material delgado.
- E7014:
- Tipo: Electrodo rutilo-celulósico con bajo contenido de hidrógeno.
- Características: Este electrodo ofrece una buena penetración y un arco estable, lo que lo hace adecuado para soldar materiales delgados con polaridad inversa. Proporciona una fusión sólida entre el metal de relleno y el material base, manteniendo una alta calidad en la soldadura.
- Aplicaciones: Se utiliza en una variedad de aplicaciones, incluida la construcción naval, la fabricación de maquinaria y la industria de estructuras metálicas, donde se requiere una alta calidad de soldadura en materiales delgados.
- E308L:
- Tipo: Electrodo de acero inoxidable para soldar materiales inoxidables delgados.
- Características: Este electrodo está diseñado específicamente para soldar aceros inoxidables delgados, ofreciendo una fusión precisa y controlada en estos materiales. Proporciona una excelente resistencia a la corrosión y una unión duradera en aplicaciones donde se requiere resistencia a la oxidación.
- Aplicaciones: Se utiliza en la fabricación de productos alimenticios, equipos médicos, componentes de la industria química y otras aplicaciones donde se requiere soldar aceros inoxidables delgados con polaridad inversa.
Los electrodos E6013, E7014 y E308L son opciones recomendadas para soldar materiales delgados con polaridad inversa.
Cada uno ofrece características específicas que los hacen adecuados para diferentes tipos de materiales y aplicaciones, garantizando soldaduras de alta calidad y duraderas en materiales delgados.
Recomendaciones adicionales
Además de seleccionar los electrodos adecuados, existen varias recomendaciones adicionales que pueden mejorar la calidad y la integridad de las soldaduras en materiales delgados con polaridad inversa:
- Ajustar la corriente: Es crucial utilizar una corriente de soldadura adecuada al trabajar con materiales delgados. Una corriente demasiado alta puede sobrecalentar el material y causar quemaduras o perforaciones, mientras que una corriente demasiado baja puede resultar en una penetración insuficiente y una unión deficiente. Se recomienda ajustar la corriente a un nivel bajo para evitar dañar el material delgado y asegurar una soldadura de calidad.
- Utilizar una técnica adecuada: Mantener un arco corto y una velocidad de avance constante es fundamental al soldar materiales delgados. Un arco demasiado largo puede generar demasiado calor y aumentar el riesgo de penetración excesiva, mientras que una velocidad de avance inconsistente puede causar irregularidades en la soldadura. Se recomienda mantener un arco corto y una velocidad de avance constante para garantizar una fusión adecuada del metal de relleno con el material base y evitar la distorsión del material.
- Practicar: Antes de soldar el material final, es recomendable practicar en una pieza similar para familiarizarse con la técnica de soldadura y ajustar la configuración adecuada de la máquina de soldadura. La práctica previa permite al soldador perfeccionar su técnica y abordar cualquier desafío específico que pueda surgir al soldar materiales delgados. Esto puede ayudar a minimizar los errores y mejorar la calidad de las soldaduras en el material final.
Ajustar la corriente de soldadura, utilizar una técnica adecuada y practicar antes de soldar el material final son recomendaciones adicionales importantes para lograr soldaduras de alta calidad en materiales delgados con polaridad inversa.
Al seguir estas recomendaciones, los soldadores pueden mejorar la precisión, la consistencia y la integridad de las soldaduras, garantizando resultados óptimos en aplicaciones donde se requiere una alta calidad y fiabilidad en la unión.
Conclusiones sobre en qué polaridad soldar materiales delgados
En conclusión, al soldar materiales delgados, la elección de la polaridad correcta es crucial para garantizar soldaduras de alta calidad y evitar daños en el material base.
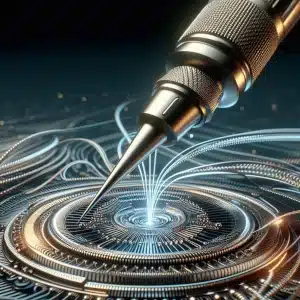
Aquí hay algunas conclusiones sobre en qué polaridad soldar materiales delgados:
- Polaridad inversa (electrodo negativo):
- Es preferible para soldar materiales delgados debido a su capacidad para reducir la penetración de calor en el material base.
- Produce un arco más estable y concentrado, lo que facilita el control del proceso de soldadura.
- Ayuda a minimizar la distorsión del material y reduce el riesgo de deformación térmica.
- Proporciona una transferencia de metal de relleno más suave y controlada, lo que es beneficioso para materiales delgados donde se requiere precisión en la soldadura.
- Recomendaciones adicionales:
- Ajustar la corriente de soldadura a un nivel bajo para evitar quemar el material delgado.
- Utilizar una técnica adecuada, manteniendo un arco corto y una velocidad de avance constante.
- Practicar antes de soldar el material final para familiarizarse con la técnica y ajustar la configuración de la máquina de soldadura.
En resumen, la polaridad inversa es la opción preferida para soldar materiales delgados soldadoras inverter debido a sus beneficios en términos de control del calor, estabilidad del arco y reducción de la distorsión del material.
Sin embargo, es importante complementar esta elección con ajustes adecuados de corriente, técnica de soldadura y práctica para garantizar soldaduras de alta calidad y una integridad estructural óptima en materiales delgados.
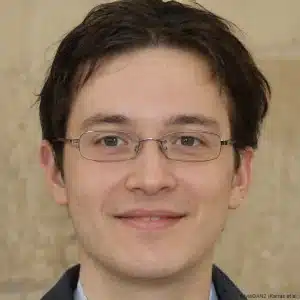
Con más de 25 años de experiencia en el sector de las ventas de equipamiento para el hogar, herramientas de bricolaje, y en los últimos 15 años en una empresa de reformas de albañilería, venta de azulejos y materiales de construcción, estufas leña, pellets, chimeneas, sistemas de calefacción.
Máster Técnico Superior en riesgos laborales.
Licenciado por la Universidad de Alicante ua.es