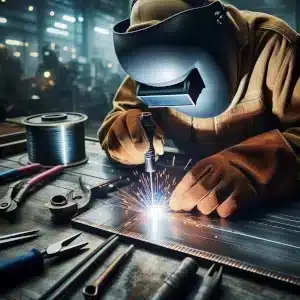
El tipo de soldadura más recomendado para soldar chapas finas es la soldadura por arco metálico con gas (GMAW), también conocida como MIG.
En el mundo de la fabricación y la construcción, la unión de chapas finas es una tarea fundamental que requiere precisión, destreza y la elección adecuada de técnicas de soldadura.
Las chapas finas se encuentran comúnmente en una variedad de aplicaciones, desde la fabricación de carrocerías de automóviles hasta la construcción de estructuras ligeras y componentes electrónicos.
En este artículo, exploraremos las diversas opciones de soldadura disponibles para unir chapas finas, centrándonos en la comparación de técnicas populares como la soldadura MIG, TIG, por arco con electrodo revestido, por puntos y por láser.
Analizaremos las ventajas y desventajas de cada método, así como sus aplicaciones específicas, con el objetivo de ayudar a los lectores a tomar decisiones informadas sobre la mejor técnica para sus proyectos.
Desde la eficiencia en la producción hasta la calidad estética de las soldaduras, este artículo proporcionará una visión integral del arte de unir chapas finas mediante soldadura.
¿Por qué la soldadura MIG es la más recomendada para soldar chapas finas?
La soldadura MIG (o GMAW) es, de hecho, una excelente opción para soldar chapas finas. Las ventajas que proporciona, como precisión, menor distorsión, limpieza en las soldaduras, eficiencia, versatilidad y facilidad de aprendizaje, la hacen ideal para este tipo de aplicaciones.
Su capacidad para controlar el calor de forma precisa y su capacidad para producir soldaduras limpias y uniformes son especialmente beneficiosas al trabajar con materiales delgados.
Seguidamente lo desarrollamos:
Precisión
La precisión en la soldadura MIG (GMAW) se refiere a la capacidad de controlar de manera exacta tanto la cantidad de calor aplicada como la cantidad de metal depositado durante el proceso de soldadura.
Esto se logra principalmente a través de la capacidad de ajustar y controlar varios parámetros del proceso, como la corriente de soldadura, la velocidad de alimentación del alambre y el flujo de gas de protección.
- Control de la corriente de soldadura: La corriente eléctrica utilizada en la soldadura MIG determina la cantidad de calor generada en el arco eléctrico. Al ajustar con precisión la corriente, es posible controlar la cantidad de calor aplicada a la chapa. Para chapas finas, donde es crucial evitar el sobrecalentamiento, este control fino es esencial para mantener la integridad del material y prevenir deformaciones no deseadas.
- Velocidad de alimentación del alambre: La soldadura MIG utiliza un electrodo de alambre continuo que se alimenta automáticamente a través del sistema de alimentación. Ajustar la velocidad de alimentación del alambre permite controlar la cantidad de metal depositado en la soldadura. Esto es especialmente importante en chapas finas, donde el exceso de metal depositado puede provocar la perforación de la chapa o un exceso de material que puede ser difícil de manejar.
- Flujo de gas de protección: El gas de protección utilizado en la soldadura MIG tiene la función de proteger el baño de fusión y el electrodo de contaminantes atmosféricos como oxígeno y nitrógeno, que podrían afectar la calidad de la soldadura. Al controlar con precisión el flujo de gas y la composición del gas de protección, se asegura un ambiente adecuado para la soldadura, lo que contribuye a mantener la calidad y la precisión del proceso.
En conjunto, el control preciso de estos parámetros permite a los soldadores ajustar la soldadura MIG de manera que se adapte perfectamente a las necesidades específicas de las chapas finas.
Esto reduce significativamente el riesgo de quemaduras o perforaciones en la chapa, ya que se puede aplicar la cantidad justa de calor y metal para lograr una soldadura limpia y de alta calidad.
Menor distorsión
La soldadura MIG (GMAW) se destaca por generar calor de forma más localizada en comparación con otros métodos de soldadura, lo que contribuye a reducir la distorsión en las chapas finas.
Esta característica es fundamental para mantener la integridad estructural y la precisión dimensional de las piezas soldadas.
Aquí hay varios aspectos que contribuyen a una menor distorsión:
- Zona afectada por el calor (HAZ) controlada: En la soldadura MIG, el calor se concentra principalmente en el área cercana al arco eléctrico y al baño de fusión. Esto significa que la zona afectada por el calor (HAZ) en la chapa es más pequeña en comparación con otros procesos de soldadura. Como resultado, se minimiza la transferencia de calor a áreas distantes de la zona de soldadura, lo que reduce el riesgo de deformación en las regiones circundantes.
- Mayor velocidad de enfriamiento: Debido a que el calor aplicado es más localizado, la velocidad de enfriamiento en la zona afectada por el calor es más rápida. Esto puede ayudar a evitar la acumulación de tensión térmica en la chapa, lo que a su vez reduce la probabilidad de deformación durante el proceso de soldadura y después de que se completa.
- Menor aporte de calor total: La soldadura MIG permite un control más preciso del calor aplicado en comparación con otros métodos. Esto significa que se puede utilizar la cantidad justa de energía térmica necesaria para fundir el material y formar una soldadura sólida, sin sobrecalentar la chapa. Al limitar el aporte total de calor, se reduce la probabilidad de distorsión debido a la expansión y contracción térmica excesiva.
- Control de la velocidad de avance: En la soldadura MIG, los soldadores pueden ajustar la velocidad de avance del cordón de soldadura con precisión. Una velocidad de avance adecuada garantiza que el calor se distribuya de manera uniforme a lo largo de la junta de soldadura, lo que contribuye a minimizar las tensiones residuales y, por lo tanto, la distorsión en la chapa.
La soldadura MIG ofrece un control superior sobre el calor aplicado, lo que se traduce en una menor distorsión en las chapas finas.
Esto ayuda a mantener la precisión dimensional de las piezas y a garantizar la calidad de la soldadura en aplicaciones donde la distorsión mínima es crítica.
Soldaduras limpias
La soldadura MIG (GMAW) es conocida por producir cordones de soldadura limpios y uniformes, con una reducida cantidad de salpicaduras.
Estas características son altamente deseables en la soldadura de chapas finas por varias razones:
- Control preciso del arco eléctrico: En la soldadura MIG, el arco eléctrico se establece de manera controlada entre el electrodo de alambre continuo y el material base. Este control permite mantener un arco estable y consistente a lo largo de la soldadura, lo que resulta en un cordón de soldadura más uniforme y de mejor calidad.
- Protección del gas de soldadura: Durante el proceso de soldadura MIG, se utiliza un gas de protección inerte o activo para proteger el baño de fusión y el electrodo de contaminantes atmosféricos. Esta atmósfera controlada alrededor del arco minimiza la formación de óxidos y otros contaminantes que podrían afectar la calidad del cordón de soldadura.
- Alambre de soldadura de alta calidad: El alambre de soldadura utilizado en la soldadura MIG está diseñado específicamente para proporcionar una alimentación suave y constante, lo que contribuye a la formación de un cordón de soldadura limpio y uniforme. Además, la composición química y el diámetro del alambre se seleccionan cuidadosamente para adaptarse al material base y a las condiciones de soldadura específicas.
- Control de la velocidad de alimentación del alambre: Los soldadores pueden ajustar la velocidad de alimentación del alambre de soldadura según sea necesario para mantener un arco estable y una deposición de metal uniforme. Esto ayuda a evitar irregularidades en el cordón de soldadura y minimiza las posibilidades de salpicaduras.
- Tecnología de soldadura avanzada: Con los avances en la tecnología de soldadura, los equipos modernos de soldadura MIG están equipados con características adicionales, como modos de arco pulsado o sistemas de control de voltaje, que ayudan a mejorar aún más la calidad de la soldadura y a reducir las salpicaduras.
En conjunto, estos factores contribuyen a producir cordones de soldadura más limpios y uniformes en la soldadura MIG, lo que es especialmente beneficioso al trabajar con chapas finas donde la estética y la calidad del acabado son importantes.
Esto también puede reducir la necesidad de trabajo de limpieza adicional después de la soldadura, lo que ahorra tiempo y esfuerzo.
Eficiencia
La soldadura MIG (GMAW) es altamente eficiente y adecuada para la producción en serie debido a varias características que la hacen rápida y rentable:
- Alta velocidad de soldadura: La soldadura MIG permite una alta velocidad de deposición de metal, lo que significa que se pueden realizar soldaduras rápidas en comparación con otros métodos de soldadura. Esto es especialmente beneficioso en aplicaciones de producción en serie donde se requiere una alta tasa de producción.
- Proceso semiautomático o automático: La soldadura MIG se puede realizar de manera semiautomática o totalmente automática utilizando equipos especializados como robots de soldadura. Esto permite una mayor eficiencia al eliminar la necesidad de mano de obra intensiva en el proceso de soldadura, lo que reduce los costos laborales y aumenta la velocidad de producción.
- Menor preparación de las piezas: La soldadura MIG es menos exigente en términos de preparación de las piezas a soldar en comparación con otros procesos de soldadura, como la soldadura TIG. Esto se debe a que la soldadura MIG es menos sensible a la limpieza y el ajuste preciso de las piezas. Como resultado, se requiere menos tiempo para preparar las piezas antes de la soldadura, lo que contribuye a una mayor eficiencia en la producción.
- Menos tiempo de limpieza y postprocesamiento: La soldadura MIG produce menos salpicaduras y escoria en comparación con otros procesos de soldadura, lo que significa que se requiere menos tiempo para limpiar y realizar trabajos de postprocesamiento después de la soldadura. Esto reduce el tiempo de inactividad de la máquina y aumenta la eficiencia general del proceso de fabricación.
En conjunto, estas características hacen que la soldadura MIG sea una opción altamente eficiente para la producción en serie en una amplia variedad de aplicaciones industriales.
La combinación de alta velocidad de soldadura, procesos semiautomáticos o automáticos, menor preparación de las piezas y menor tiempo de limpieza y postprocesamiento la convierte en una opción económica y rentable para la fabricación en masa.
Versatilidad
La soldadura MIG (GMAW) es ampliamente reconocida por su versatilidad, ya que puede utilizarse para soldar una variedad de materiales, lo que la convierte en una opción popular en numerosas industrias.
Aquí se detallan algunas razones de su versatilidad:
- Diversidad de materiales: La soldadura MIG puede utilizarse para soldar una amplia gama de materiales metálicos, incluyendo acero al carbono, acero inoxidable, aluminio, cobre, níquel y sus aleaciones. Esta capacidad para adaptarse a diferentes materiales la hace adecuada para una variedad de aplicaciones industriales.
- Compatibilidad con diferentes espesores: La soldadura MIG es adecuada para soldar materiales de diferentes espesores, desde chapas delgadas hasta piezas más gruesas. Esto la hace útil en una variedad de aplicaciones donde se requiere unir materiales de diferentes grosores.
- Variedad de gases de protección: La soldadura MIG puede utilizarse con una variedad de gases de protección, lo que permite adaptar el proceso a las necesidades específicas del material y la aplicación. Por ejemplo, se pueden usar gases inertes como el argón o el helio para la soldadura de aluminio, mientras que se pueden usar mezclas de gases activos e inertes para mejorar la penetración y la estabilidad del arco en aceros al carbono.
- Flexibilidad en la configuración del equipo: Los equipos de soldadura MIG son altamente adaptables y pueden configurarse para diferentes aplicaciones y materiales. Por ejemplo, se pueden cambiar fácilmente los tipos de alambre de soldadura y los diámetros del alambre para adaptarse a los requisitos específicos del material y del proceso de soldadura.
- Soldadura en diferentes posiciones: La soldadura MIG es versátil en términos de la posición en la que se puede realizar la soldadura. Puede ser utilizada en posición plana, vertical, horizontal o sobrecabeza, lo que la hace adecuada para una amplia variedad de configuraciones de trabajo.
La soldadura MIG ofrece una versatilidad excepcional al ser compatible con una amplia gama de materiales, espesores y condiciones de trabajo.
Esta capacidad para adaptarse a diferentes requisitos la convierte en una opción preferida en numerosas aplicaciones industriales donde se requiere flexibilidad y eficiencia en el proceso de soldadura.
Facilidad de aprendizaje
La soldadura MIG (GMAW) es conocida por su relativa facilidad de aprendizaje, lo que la hace accesible para una amplia gama de usuarios, desde principiantes hasta soldadores experimentados.
Algunas razones que respaldan esta afirmación son:
- Simplicidad del proceso: En comparación con otros métodos de soldadura, como la soldadura TIG o la soldadura por arco sumergido, la soldadura MIG es relativamente simple de aprender y dominar. El proceso implica alimentar un alambre de metal continuo a través de una pistola de soldadura que suministra un gas de protección para crear el arco eléctrico y fundir el metal base. Esta simplicidad de operación hace que la soldadura MIG sea más fácil de comprender para los principiantes.
- Control automático de ciertos parámetros: Los soldadores MIG modernos a menudo están equipados con características de control automático que ayudan a mantener parámetros críticos, como la corriente de soldadura y la velocidad de alimentación del alambre, dentro de rangos óptimos. Esto simplifica el proceso para los soldadores novatos al reducir la necesidad de ajustes manuales complicados.
- Equipos modernos: Los avances en la tecnología de soldadura, como los soldadores inverter, han hecho que la soldadura MIG sea aún más accesible para los principiantes. Los soldadores inverter son más compactos, ligeros y eficientes en comparación con los equipos de soldadura convencionales, lo que facilita su transporte y uso en una variedad de entornos. Además, su capacidad para proporcionar una corriente de salida estable y controlada mejora la calidad de la soldadura y simplifica el proceso para los aprendices.
- Amplio acceso a recursos de aprendizaje: Con la proliferación de recursos de aprendizaje en línea, videos instructivos y cursos de capacitación, los principiantes pueden acceder fácilmente a información detallada sobre cómo realizar soldaduras MIG correctamente. Esto les permite aprender y mejorar sus habilidades a su propio ritmo, independientemente de su ubicación geográfica o experiencia previa en soldadura.
La soldadura MIG es una técnica relativamente fácil de aprender, especialmente con la ayuda de equipos modernos como los soldadores inverter y el acceso a una amplia gama de recursos de aprendizaje.
Esta accesibilidad hace que la soldadura MIG sea una opción atractiva tanto para los principiantes como para los soldadores experimentados que buscan mejorar sus habilidades.
Otros tipos de soldadura para soldar chapas finas
La soldadura MIG no es la única opción para soldar chapas finas. Hay varias técnicas alternativas que también pueden ser consideradas, dependiendo de los requisitos específicos del proyecto y las habilidades del soldador.
Aquí se describen algunas de estas alternativas:
- Soldadura TIG (GTAW):
- La soldadura TIG es conocida por ofrecer un alto nivel de precisión y control del calor, lo que la hace adecuada para trabajar con materiales delgados.
- Permite soldaduras limpias y de alta calidad con una apariencia estética superior.
- Sin embargo, la soldadura TIG requiere más habilidad y experiencia por parte del soldador debido a la necesidad de controlar simultáneamente la antorcha de soldadura, el electrodo de tungsteno y el aporte de material de relleno.
- Soldadura por arco con electrodo revestido (SMAW):
- La soldadura SMAW es una técnica versátil y ampliamente utilizada que puede aplicarse a una variedad de materiales y espesores, incluyendo chapas finas.
- Es económica y no requiere equipos costosos.
- Sin embargo, puede generar más distorsión y salpicaduras en comparación con la soldadura MIG, lo que puede requerir más tiempo de limpieza y postprocesamiento.
- Soldadura por puntos:
- La soldadura por puntos es ideal para unir chapas finas de forma rápida y precisa, con mínima deformación.
- Es comúnmente utilizada en la industria automotriz para unir láminas metálicas en la fabricación de carrocerías y componentes eléctricos.
- Sin embargo, la soldadura por puntos puede no ser tan versátil como otras técnicas, ya que está limitada a unir materiales en áreas específicas.
- Soldadura por láser:
- La soldadura por láser ofrece una alta precisión y un mínimo de distorsión en chapas finas.
- Es adecuada para aplicaciones donde se requiere una calidad excepcional y tolerancias muy ajustadas.
- Sin embargo, la soldadura por láser tiende a ser más costosa y requiere equipos especializados y un alto nivel de experiencia técnica para su operación.
Cada una de estas técnicas de soldadura tiene sus propias ventajas y desventajas, y la elección de la técnica adecuada dependerá de una variedad de factores, incluyendo las especificaciones del proyecto, el presupuesto, la disponibilidad de equipos y la experiencia del soldador.
Conclusiones sobre el mejor tipo de soldadura para soldar chapas finas
La elección del mejor tipo de soldadura para soldar chapas finas dependerá de una serie de factores, incluyendo las especificaciones del proyecto, las habilidades del soldador, el equipo disponible y los requisitos de calidad.
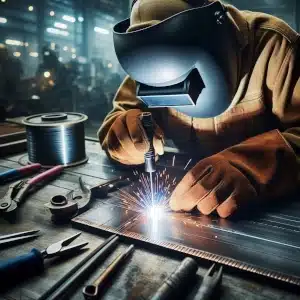
A continuación, se presentan algunas conclusiones clave:
- Soldadura MIG (GMAW):
- Es una opción altamente recomendada debido a su precisión, control del calor y velocidad de soldadura.
- Ofrece cordones de soldadura limpios y uniformes, con menor riesgo de distorsión y deformación en las chapas finas.
- Es especialmente adecuada para aplicaciones de producción en serie debido a su eficiencia y versatilidad en una amplia gama de materiales.
- Soldadura TIG (GTAW):
- Ofrece un alto nivel de precisión y control del calor, lo que la hace ideal para aplicaciones donde se requiere una soldadura de alta calidad y estética.
- Requiere más habilidad y experiencia por parte del soldador en comparación con la soldadura MIG.
- Soldadura por arco con electrodo revestido (SMAW):
- Es una técnica versátil y económica, adecuada para una variedad de materiales y espesores, incluyendo chapas finas.
- Puede generar más distorsión y salpicaduras en comparación con la soldadura MIG.
- Soldadura por puntos:
- Es ideal para unir chapas finas de forma rápida y precisa, con mínima deformación.
- Sin embargo, puede no ser tan versátil como otras técnicas y está limitada a unir materiales en áreas específicas.
- Soldadura por láser:
- Ofrece una alta precisión y un mínimo de distorsión en chapas finas, adecuada para aplicaciones donde se requiere una calidad excepcional y tolerancias ajustadas.
- Sin embargo, tiende a ser más costosa y requiere equipos especializados y un alto nivel de experiencia técnica.
En conclusión, la soldadura MIG es generalmente la opción preferida para soldar chapas finas debido a su combinación de precisión, control del calor, eficiencia y versatilidad.
Sin embargo, otras técnicas de soldadura pueden ser adecuadas en situaciones específicas, dependiendo de los requisitos del proyecto y las capacidades disponibles.
Es importante evaluar cuidadosamente cada opción antes de tomar una decisión final.
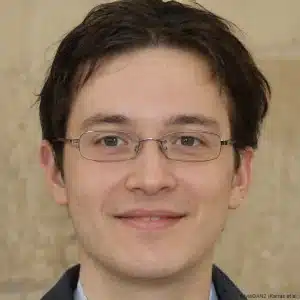
Con más de 25 años de experiencia en el sector de las ventas de equipamiento para el hogar, herramientas de bricolaje, y en los últimos 15 años en una empresa de reformas de albañilería, venta de azulejos y materiales de construcción, estufas leña, pellets, chimeneas, sistemas de calefacción.
Máster Técnico Superior en riesgos laborales.
Licenciado por la Universidad de Alicante ua.es