
En este artículo, exploraremos en detalle las diferencias entre las máquinas de soldar TIG y MIG, desde sus principios básicos hasta sus ventajas, desventajas y aplicaciones en diversos campos industriales.
Al comprender las diferencias clave entre estos dos procesos de soldadura, los profesionales y aficionados por igual podrán tomar decisiones informadas sobre cuál método es el más adecuado para sus necesidades específicas.
En el mundo de la soldadura, la elección del proceso adecuado es crucial para lograr resultados óptimos en términos de calidad, eficiencia y rendimiento.
Dos de los métodos más comunes y populares en la soldadura son el TIG (Tungsten Inert Gas) y el MIG (Metal Inert Gas), cada uno con sus propias características distintivas y aplicaciones específicas.
Las máquinas de soldar TIG (Tungsten Inert Gas) y MIG (Metal Inert Gas) son dos tipos populares de equipos de soldadura utilizados en diversas aplicaciones.
Aquí hay algunas diferencias clave entre ellas:
Proceso de soldadura
El proceso de soldadura es una técnica fundamental en la fabricación y construcción de una amplia variedad de productos y estructuras metálicas.
Consiste en unir dos o más piezas de metal mediante la aplicación de calor y/o presión, formando una unión permanente entre ellas.
Existen varios métodos de soldadura, cada uno con sus propias características, ventajas y aplicaciones específicas.
En esta sección, exploraremos dos de los procesos de soldadura más comunes y ampliamente utilizados: TIG (Tungsten Inert Gas) y MIG (Metal Inert Gas).
Mediante un análisis detallado, examinaremos cómo funcionan estos procesos, sus diferencias clave y sus aplicaciones típicas en la industria.
Proceso TIG (Tungsten Inert Gas):
- Electrodo de Tungsteno: En el proceso TIG, se utiliza un electrodo de tungsteno no consumible que se sujeta en una antorcha de soldadura especializada. El tungsteno tiene un punto de fusión muy alto y no se consume durante el proceso de soldadura.
- Arco Eléctrico: Cuando el electrodo de tungsteno se acerca al material base, se crea un arco eléctrico entre el electrodo y la pieza de trabajo. Este arco eléctrico genera altas temperaturas que funden tanto el electrodo como el metal base, formando un charco de soldadura.
- Gas Inerte: Para proteger el área de soldadura de la contaminación atmosférica, se utiliza un gas inerte como argón o helio. Este gas inerte fluye continuamente desde la antorcha de soldadura hacia el área de soldadura, creando un ambiente libre de oxígeno y nitrógeno que evita la formación de óxidos y otras impurezas en el cordón de soldadura.
- Control Manual: Durante el proceso TIG, el soldador controla manualmente la velocidad de avance, la posición del electrodo y la forma del cordón de soldadura. Esto requiere un alto nivel de habilidad y precisión por parte del soldador para garantizar una soldadura de calidad.
Proceso MIG (Metal Inert Gas):
- Electrodo Consumible: En el proceso MIG, se utiliza un electrodo consumible que se alimenta automáticamente desde un carrete a través de la antorcha de soldadura. Este electrodo está hecho del mismo material que se está soldando y se consume durante el proceso de soldadura.
- Arco Eléctrico: Al igual que en el proceso TIG, cuando el electrodo se acerca al material base, se genera un arco eléctrico que funde el electrodo y el metal base, formando un charco de soldadura.
- Gas Inerte o Mezcla de Gases: Se utiliza un gas inerte, como argón o una mezcla de gases, para proteger el arco y la soldadura de la contaminación atmosférica. Este gas fluye desde la antorcha de soldadura hacia el área de soldadura, creando un ambiente protector similar al proceso TIG.
- Alimentación Automática del Electrodo: A diferencia del proceso TIG, en el proceso MIG, el electrodo se alimenta automáticamente desde un carrete a través de la antorcha de soldadura. Esto simplifica el proceso y hace que la soldadura sea más rápida y fácil de realizar, lo que lo hace adecuado para aplicaciones de producción en serie.
Aunque ambos procesos utilizan un gas inerte para proteger la soldadura, difieren en el tipo de electrodo utilizado (no consumible en TIG y consumible en MIG) y en la forma en que se alimenta el electrodo durante la soldadura.
Esto resulta en diferencias significativas en la forma en que se controla y realiza cada proceso de soldadura.
Tipo de soldadura
El tipo de soldadura utilizado en un proyecto específico depende en gran medida de los materiales a unir, el grosor del metal y las exigencias de precisión.
Tanto el proceso TIG como el MIG ofrecen ventajas y aplicaciones distintas:
TIG (Tungsten Inert Gas):
El proceso de soldadura TIG es altamente versátil y adecuado para una amplia gama de materiales, lo que lo convierte en una opción popular en numerosas aplicaciones industriales y de fabricación.
Algunas de sus características y aplicaciones incluyen:
- Variedad de materiales: TIG es compatible con una amplia gama de materiales, como acero inoxidable, aluminio, cobre y aleaciones de níquel. Esta versatilidad lo hace ideal para entornos donde se utilizan múltiples tipos de metales.
- Soldadura de materiales delgados: TIG es especialmente adecuado para soldar materiales delgados debido a su capacidad para proporcionar un arco de soldadura preciso y controlado. Esta precisión es esencial en aplicaciones donde se requiere una alta calidad de acabado y una soldadura limpia, como la fabricación de equipos electrónicos o la industria aeroespacial.
- Alta precisión: Debido al control fino del arco y la capacidad de ajustar la corriente de soldadura y el flujo de gas, TIG es ideal para aplicaciones que requieren un alto nivel de precisión y detalle, como la soldadura de tuberías o componentes de precisión en la industria médica.
MIG (Metal Inert Gas):
El proceso de soldadura MIG, aunque también versátil, se utiliza principalmente en aplicaciones industriales donde se sueldan metales más gruesos y se prioriza la eficiencia en la producción.
Algunas de sus características y aplicaciones incluyen:
- Soldadura de acero: MIG es particularmente adecuado para soldar acero, incluyendo acero al carbono y acero inoxidable. Es ampliamente utilizado en la fabricación industrial para la producción en serie de componentes metálicos.
- Soldadura de metal grueso: Debido a su capacidad para depositar rápidamente grandes cantidades de metal de soldadura, MIG es eficiente para unir metales más gruesos. Esto lo hace ideal para aplicaciones donde se requiere una alta velocidad de producción, como la fabricación de estructuras metálicas.
- Facilidad de uso y productividad: MIG es relativamente fácil de aprender y usar en comparación con TIG, lo que lo hace popular en entornos de fabricación donde se requiere una alta productividad y eficiencia de mano de obra.
Mientras que TIG destaca en la soldadura de materiales delgados y aplicaciones de alta precisión, MIG es preferido en la soldadura de metales más gruesos y entornos de producción industrial donde la eficiencia es primordial.
La elección entre estos dos procesos depende de las necesidades específicas del proyecto, el tipo de material y los requisitos de calidad.
Control y habilidades requeridas
El nivel de habilidad y destreza necesarios para realizar soldaduras exitosas varía significativamente entre los procesos de soldadura TIG y MIG.
A continuación, se detallan las diferencias en cuanto al control y las habilidades necesarias para cada uno:
TIG (Tungsten Inert Gas):
El proceso de soldadura TIG requiere un alto nivel de habilidad y precisión por parte del soldador debido a la necesidad de controlar varios parámetros simultáneamente.
Algunos aspectos importantes a considerar son:
- Control manual del arco: En TIG, el soldador debe mantener el arco eléctrico entre el electrodo de tungsteno y el material base de manera constante y uniforme. Esto requiere una mano firme y una coordinación precisa para controlar la distancia entre el electrodo y el material.
- Ajuste de la corriente de soldadura: El soldador debe ser capaz de ajustar la corriente de soldadura de manera adecuada según el tipo y grosor del material a soldar. Esto afecta directamente la penetración y calidad de la soldadura.
- Regulación del flujo de gas: El gas inerte utilizado en el proceso TIG (generalmente argón o helio) es crucial para proteger el área de soldadura de la contaminación atmosférica. El soldador debe controlar el flujo de gas para garantizar una protección adecuada y una soldadura limpia.
MIG (Metal Inert Gas):
En comparación con TIG, el proceso MIG es más fácil de aprender y de usar, lo que lo hace más adecuado para aplicaciones de producción en serie.
Algunos aspectos clave en cuanto al control y habilidades requeridas en MIG son:
- Control automático del electrodo y el gas: En MIG, la máquina controla automáticamente la alimentación del electrodo y el flujo de gas, lo que reduce la necesidad de ajustes manuales por parte del soldador. Esto simplifica significativamente el proceso y hace que sea más fácil de manejar para los principiantes.
- Concentración en la técnica de movimiento: Aunque el control del arco es menos exigente en MIG en comparación con TIG, el soldador aún debe dominar la técnica de movimiento de la antorcha para lograr una soldadura uniforme y de alta calidad. Esto implica mover la antorcha de soldadura a una velocidad y ángulo adecuados para depositar el metal de manera uniforme.
- Atención a la configuración de la máquina: Aunque la máquina de soldadura MIG controla automáticamente la mayoría de los parámetros, el soldador aún debe prestar atención a la configuración adecuada de la máquina, como la selección del tipo de gas y la velocidad de alimentación del alambre, para garantizar resultados óptimos.
Mientras que TIG requiere un mayor nivel de habilidad manual y control por parte del soldador, MIG es más fácil de aprender y de usar gracias a su mayor automatización.
La elección entre ambos procesos dependerá de las necesidades específicas de la aplicación y del nivel de habilidad del operador.
Calidad del cordón de soldadura
La calidad del cordón de soldadura es un aspecto crucial en cualquier proyecto de soldadura, ya que afecta directamente la resistencia, durabilidad y apariencia estética de la unión.
Tanto el proceso TIG como el MIG tienen impactos distintos en la calidad del cordón de soldadura:
TIG (Tungsten Inert Gas):
El proceso TIG es conocido por producir cordones de soldadura de alta calidad y estética superior.
Algunas de sus características clave incluyen:
- Limpieza y precisión: TIG proporciona un arco de soldadura altamente controlado, lo que resulta en cordones limpios y bien definidos. La capacidad de controlar la temperatura y la velocidad de avance permite una soldadura precisa, especialmente en aplicaciones donde se requiere una apariencia estética y detalles finos.
- Menos salpicaduras y escoria: Debido a la naturaleza controlada del arco de soldadura en el proceso TIG, hay menos salpicaduras y escoria generadas durante el proceso. Esto significa que se requiere menos limpieza posterior a la soldadura, lo que contribuye a un acabado más limpio y profesional.
- Adecuado para aplicaciones de alta calidad: TIG es ideal para aplicaciones que requieren una soldadura de alta calidad, como la fabricación de equipos médicos, la industria aeroespacial y la joyería, donde la apariencia estética y la integridad estructural son fundamentales.
MIG (Metal Inert Gas):
Si bien el proceso MIG es eficiente y versátil, puede presentar algunos desafíos en cuanto a la calidad del cordón de soldadura, especialmente en términos estéticos.
Algunas características de la calidad del cordón en MIG son:
- Mayor tendencia a las salpicaduras: Debido a la velocidad de deposición más alta y la forma en que se alimenta el material de relleno, el proceso MIG tiende a producir más salpicaduras durante la soldadura en comparación con TIG. Estas salpicaduras pueden afectar la apariencia estética del cordón y requerirán más limpieza y acabado posterior.
- Posible presencia de escoria: Aunque el proceso MIG tiende a generar menos escoria en comparación con otros métodos de soldadura, aún puede dejar una pequeña cantidad de escoria en la superficie del cordón de soldadura. Esto puede afectar la apariencia y la integridad de la soldadura, especialmente en aplicaciones donde se requiere un acabado estético de alta calidad.
- Adecuado para aplicaciones de producción: A pesar de estos desafíos, MIG sigue siendo ampliamente utilizado en aplicaciones de fabricación donde la eficiencia y la velocidad de producción son prioritarias sobre la estética, como la construcción de estructuras metálicas, la fabricación de automóviles y la industria de fabricación en general.
Aunque tanto TIG como MIG son capaces de producir soldaduras fuertes y eficientes, el proceso TIG es generalmente preferido en aplicaciones que requieren una alta calidad estética y una precisión fina, mientras que el MIG es más adecuado para aplicaciones de producción donde la velocidad y la eficiencia son prioritarias sobre la apariencia estética.
Electrodo
El electrodo desempeña un papel fundamental en el proceso de soldadura tanto en TIG como en MIG, aunque difieren significativamente en su naturaleza y función:
TIG (Tungsten Inert Gas):
En el proceso TIG, se utiliza un electrodo de tungsteno no consumible. Este electrodo actúa como una fuente de calor y un conductor eléctrico para generar el arco de soldadura.
Algunas características importantes del electrodo de tungsteno en el proceso TIG incluyen:
- No consumible: A diferencia de otros tipos de electrodos utilizados en otros procesos de soldadura, el electrodo de tungsteno en TIG no se consume durante la soldadura. En su lugar, el metal de relleno se agrega al cordón de soldadura por separado.
- Alta resistencia a la temperatura: El tungsteno es capaz de soportar temperaturas extremadamente altas sin fundirse, lo que lo hace ideal para generar el arco de soldadura en el proceso TIG, donde las temperaturas pueden alcanzar varios miles de grados Celsius.
- Variedad de tipos y aleaciones: Los electrodos de tungsteno están disponibles en una variedad de tipos y aleaciones para adaptarse a diferentes aplicaciones y materiales base. Algunos ejemplos incluyen electrodos puros de tungsteno, así como aleaciones con adiciones de torio, cerio, lantano u otros materiales para mejorar las características de rendimiento.
MIG (Metal Inert Gas):
En el proceso MIG, se utiliza un electrodo de metal consumible que también actúa como material de relleno para unir las piezas de trabajo.
Algunas características clave del electrodo en el proceso MIG incluyen:
- Consumible: A diferencia del electrodo de tungsteno en TIG, el electrodo en MIG se consume durante el proceso de soldadura. A medida que el electrodo se alimenta hacia la zona de soldadura, se funde y se deposita como material de relleno para formar el cordón de soldadura.
- Facilidad de alimentación: Los electrodos de metal consumible en MIG suelen estar en forma de alambre y se alimentan automáticamente a través de un mecanismo de alimentación en la pistola de soldadura. Esto facilita la alimentación continua del electrodo y contribuye a una soldadura más rápida y eficiente, especialmente en aplicaciones de producción en serie.
- Variedad de materiales y diámetros: Los electrodos de metal consumible en MIG están disponibles en una amplia gama de materiales y diámetros para adaptarse a diferentes tipos de metales base y requisitos de soldadura. Los materiales comunes incluyen acero al carbono, acero inoxidable, aluminio y aleaciones de cobre, entre otros.
Mientras que el electrodo en el proceso TIG es no consumible y actúa principalmente como fuente de calor y conductor eléctrico, el electrodo en el proceso MIG es consumible y proporciona tanto la fuente de calor como el material de relleno para la soldadura.
Estas diferencias en el tipo de electrodo tienen un impacto significativo en cómo se lleva a cabo cada proceso de soldadura y en las características del cordón de soldadura resultante.
Material de relleno
En el proceso de soldadura, el material de relleno es utilizado para reforzar la unión entre las piezas de metal que están siendo soldadas.
Tanto en el proceso TIG como en el MIG, se emplea material de relleno, aunque difieren en su aplicación y forma de suministro:
TIG (Tungsten Inert Gas):
En el proceso TIG, el material de relleno se introduce en el área de soldadura mediante una varilla o alambre de aporte separado.
Esta varilla, hecha del mismo material que las piezas a unir o de un material compatible, se alimenta manualmente en el arco de soldadura por el soldador.
La varilla se funde gradualmente, añadiendo metal a la piscina de soldadura para reforzar la unión y llenar cualquier espacio entre las piezas.
Este método proporciona un control preciso sobre la cantidad de material de relleno añadido y permite ajustar la composición del cordón de soldadura según sea necesario.
MIG (Metal Inert Gas):
En contraste, en el proceso MIG, el material de relleno se suministra a través del electrodo mismo, que consiste en un alambre de metal consumible.
Este alambre de metal, que actúa simultáneamente como electrodo y material de relleno, es alimentado automáticamente a través de la antorcha de soldadura desde un carrete de alambre.
A medida que el alambre se alimenta en el arco de soldadura, se funde y se deposita en la unión, proporcionando el material necesario para formar el cordón de soldadura.
La velocidad de alimentación del alambre de relleno se ajusta para controlar la cantidad de material depositado y mantener la consistencia en la soldadura.
Aunque tanto TIG como MIG utilizan material de relleno para fortalecer la unión entre las piezas de metal, difieren en la forma en que se suministra este material.
Mientras que en TIG se emplea una varilla o alambre de aporte separado, en MIG el material de relleno se suministra a través del electrodo de metal consumible que forma parte del proceso de soldadura.
Gas protector
En los procesos de soldadura TIG y MIG, el gas protector juega un papel crucial alrededor del arco de soldadura para prevenir la contaminación atmosférica y garantizar la integridad de la soldadura.
A continuación, se detallan los tipos de gases protectores utilizados en cada proceso:
TIG (Tungsten Inert Gas):
El proceso TIG generalmente utiliza gases inertes, como argón o una mezcla de argón y dióxido de carbono (CO2), como gases protectores.
Estos gases inertes no reaccionan con los materiales base ni con el electrodo de tungsteno, lo que ayuda a proteger el área de soldadura de la oxidación y otras impurezas atmosféricas.
La selección del gas depende del material base y de las especificaciones de la soldadura.
El argón puro se utiliza comúnmente para soldar acero inoxidable y aleaciones de aluminio, mientras que las mezclas de argón y CO2 pueden ser más adecuadas para aceros al carbono.
MIG (Metal Inert Gas):
El proceso MIG puede utilizar una variedad de gases protectores, dependiendo de los materiales base y de las necesidades específicas de la soldadura.
Algunos de los gases protectores comúnmente utilizados en soldadura MIG incluyen argón, helio, dióxido de carbono (CO2), oxígeno o mezclas de estos gases.
La selección del gas protector puede influir en la penetración, la apariencia y la estabilidad del arco de soldadura.
Por ejemplo, el CO2 puro se utiliza a menudo para la soldadura de aceros al carbono debido a su mayor capacidad de penetración, mientras que las mezclas de argón y CO2 son comunes para la soldadura de acero al carbono y acero inoxidable.
Tanto en el proceso TIG como en el MIG, la elección del gas protector es crucial para garantizar una soldadura de calidad al proteger el área de soldadura de la contaminación atmosférica y controlar las características del arco de soldadura.
La selección del gas dependerá de diversos factores, como el tipo de material base, la calidad deseada de la soldadura y las especificaciones del proyecto.
Técnica
La técnica utilizada en los procesos de soldadura TIG y MIG varía en complejidad y nivel de habilidad requerido por parte del soldador:
TIG (Tungsten Inert Gas):
La técnica de soldadura TIG es conocida por su precisión y requiere un mayor nivel de habilidad y destreza por parte del soldador.
Algunas características de la técnica TIG incluyen:
- Control preciso del arco: En TIG, el soldador debe controlar cuidadosamente la distancia entre el electrodo de tungsteno y el material base para mantener un arco eléctrico estable. Esto requiere una mano firme y un control preciso para evitar que el electrodo toque la pieza de trabajo y cause cortocircuitos.
- Manejo de la varilla de aporte: Para agregar material de relleno, el soldador debe alimentar manualmente una varilla de metal en el baño de soldadura mientras controla simultáneamente el arco. Esto requiere coordinación y habilidad para mantener un flujo uniforme de material de relleno y unir las piezas de manera uniforme.
- Control del flujo de gas: Además de controlar el arco y la varilla de aporte, el soldador también debe regular el flujo de gas inerte, como argón o una mezcla de argón y CO2, para proteger el área de soldadura de la contaminación atmosférica y asegurar una soldadura limpia.
MIG (Metal Inert Gas):
En contraste, la técnica utilizada en la soldadura MIG es generalmente más sencilla y más fácil de aprender, lo que la hace ideal para principiantes y aplicaciones de producción.
Algunas características de la técnica MIG incluyen:
- Alimentación automática del electrodo y material de relleno: En MIG, el electrodo de metal consumible y el material de relleno se alimentan automáticamente a través de la pistola de soldadura, lo que elimina la necesidad de alimentación manual como en TIG. Esto simplifica el proceso y hace que sea más fácil mantener un flujo constante de material de soldadura.
- Control limitado del arco: A diferencia de TIG, donde se requiere un control preciso del arco eléctrico, en MIG el arco se mantiene automáticamente una vez que se inicia, lo que reduce la necesidad de ajustes manuales por parte del soldador.
- Menor necesidad de destreza manual: Debido a la automatización de la alimentación del electrodo y del material de relleno, la técnica de soldadura MIG requiere menos habilidades manuales y coordinación que TIG. Esto la hace más accesible para soldadores principiantes o aquellos que no tienen tanta experiencia en soldadura.
La técnica de soldadura TIG es más compleja y requiere un mayor nivel de habilidad y control por parte del soldador, mientras que la soldadura MIG es más sencilla y automatizada, lo que la hace más adecuada para principiantes y aplicaciones de producción en serie.
La elección entre los dos métodos depende de varios factores, incluyendo la habilidad del soldador, la aplicación específica y los requisitos de calidad del proyecto.
Aplicaciones
Tanto la soldadura TIG como la soldadura MIG tienen una amplia gama de aplicaciones debido a su versatilidad y capacidad para soldar una variedad de materiales.
Aquí hay un desglose de las aplicaciones típicas para cada proceso:
TIG (Tungsten Inert Gas):
La soldadura TIG es adecuada para una variedad de materiales y se utiliza en diversas industrias, incluyendo:
- Acero inoxidable: TIG es ampliamente utilizado en la fabricación de equipos médicos, productos farmacéuticos, componentes de alimentos y bebidas, y otras aplicaciones donde se requiere una alta resistencia a la corrosión y una apariencia estética.
- Aluminio: En la industria aeroespacial y automotriz, así como en la fabricación de estructuras arquitectónicas y navales, la soldadura TIG es fundamental para unir componentes de aluminio debido a su capacidad para producir soldaduras limpias y de alta calidad.
- Acero al carbono y aleaciones de acero: TIG se utiliza en la fabricación de equipos industriales, tuberías, recipientes a presión y estructuras metálicas donde se requiere una alta resistencia y una soldadura de alta calidad.
- Titanio: Debido a la alta pureza y resistencia del titanio, la soldadura TIG es esencial en aplicaciones aeroespaciales, médicas y de fabricación de productos deportivos donde se requiere una unión resistente y duradera.
MIG (Metal Inert Gas):
La soldadura MIG también tiene una amplia gama de aplicaciones y es comúnmente utilizada en las siguientes áreas:
- Acero al carbono: La soldadura MIG es ampliamente utilizada en la construcción de estructuras metálicas, fabricación de maquinaria, fabricación de vehículos y otras aplicaciones donde se requiere una unión fuerte y eficiente en la producción en masa.
- Aluminio: Aunque la soldadura MIG de aluminio puede requerir equipos especiales y técnicas específicas, es común en la industria de la construcción naval, fabricación de carrocerías de automóviles y fabricación de equipos deportivos.
- Acero inoxidable: La soldadura MIG es utilizada en la fabricación de equipos de cocina, sistemas de tuberías, tanques de almacenamiento y otros productos donde se requiere resistencia a la corrosión y una apariencia estética.
- Magnesio: En aplicaciones aeroespaciales y automotrices, la soldadura MIG se utiliza para unir componentes de magnesio debido a su ligereza y resistencia, así como su capacidad para producir soldaduras rápidas y eficientes.
Tanto la soldadura TIG como la soldadura MIG son fundamentales en una variedad de industrias y aplicaciones, y la elección entre ellas depende del tipo de material, las especificaciones del proyecto y los requisitos de calidad de la soldadura.
Ventajas
La soldadura es un proceso esencial en la fabricación y construcción de una amplia variedad de productos y estructuras metálicas.
Cada método de soldadura tiene sus propias ventajas y beneficios distintivos, que pueden influir significativamente en la elección del proceso más adecuado para una aplicación específica.
En esta sección, exploraremos las ventajas clave de dos de los métodos de soldadura más utilizados: TIG (Tungsten Inert Gas) y MIG (Metal Inert Gas).
A través de un análisis detallado, examinaremos cómo estas ventajas impactan en la calidad, eficiencia y aplicaciones de cada método de soldadura, proporcionando una visión clara de sus fortalezas y beneficios en diversos contextos industriales y de fabricación.
TIG (Tungsten Inert Gas):
- Soldaduras de alta calidad: El proceso TIG es conocido por producir soldaduras de alta calidad con una apariencia estética superior. La precisión del arco y la capacidad de controlar el material de relleno manualmente permiten obtener uniones limpias y bien definidas.
- Mayor precisión: Debido al control fino del arco eléctrico y la capacidad de ajustar la velocidad de avance y otros parámetros, el proceso TIG es ideal para aplicaciones que requieren una alta precisión y detalle, como la fabricación de equipos médicos y aeroespaciales.
- Menos salpicaduras: En comparación con otros procesos de soldadura, como MIG, TIG tiende a producir menos salpicaduras. Esto significa que se requiere menos limpieza posterior a la soldadura, lo que reduce el tiempo y los costos asociados.
MIG (Metal Inert Gas):
- Mayor velocidad de soldadura: Una de las principales ventajas de la soldadura MIG es su mayor velocidad de soldadura en comparación con TIG. Debido a la alimentación automática del electrodo y del material de relleno, se pueden lograr velocidades de soldadura más altas, lo que resulta en una mayor productividad en aplicaciones de producción en serie.
- Menos distorsión: La soldadura MIG genera menos distorsión en las piezas soldadas en comparación con otros métodos de soldadura, como la soldadura por arco manual. Esto se debe en parte a la menor cantidad de calor aplicado durante el proceso, lo que minimiza la deformación de las piezas y facilita el mantenimiento de tolerancias dimensionales precisas.
- Ideal para producción: Debido a su velocidad de soldadura y facilidad de uso, la soldadura MIG es ideal para aplicaciones de producción en serie donde se requiere una alta eficiencia y repetibilidad. Es comúnmente utilizada en la fabricación de automóviles, construcción de estructuras metálicas, y otras industrias donde se necesitan grandes volúmenes de soldadura.
TIG ofrece ventajas en términos de calidad y precisión, mientras que MIG destaca por su velocidad y eficiencia en la producción.
La elección entre los dos métodos de soldadura depende de los requisitos específicos del proyecto, incluyendo la calidad deseada, la velocidad de producción y las habilidades del operador.
Desventajas
Aunque la soldadura es un proceso esencial en la fabricación y construcción de una amplia gama de productos y estructuras metálicas, cada método de soldadura presenta desafíos y limitaciones únicas.
Es importante comprender estas desventajas para poder tomar decisiones informadas al seleccionar el método de soldadura más adecuado para una aplicación específica.
En esta sección, exploraremos las desventajas clave de dos de los métodos de soldadura más comúnmente utilizados: TIG (Tungsten Inert Gas) y MIG (Metal Inert Gas).
Al analizar estas desventajas, podemos obtener una comprensión más completa de los aspectos menos favorables de cada proceso de soldadura y cómo pueden afectar la calidad, eficiencia y aplicaciones en diversos contextos industriales y de fabricación.
TIG (Tungsten Inert Gas):
- Más difícil de aprender: La soldadura TIG requiere un mayor nivel de habilidad y destreza por parte del soldador en comparación con otros métodos de soldadura. Controlar simultáneamente la alimentación del electrodo, la velocidad de avance y el flujo de gas, mientras se mantiene el arco, puede ser desafiante para los principiantes, lo que resulta en una curva de aprendizaje más pronunciada.
- Mayor tiempo de preparación: Antes de iniciar el proceso de soldadura TIG, se requiere un tiempo adicional para preparar adecuadamente el equipo, incluyendo la configuración de la corriente de soldadura, la selección del electrodo de tungsteno y la preparación del área de soldadura. Esto puede aumentar el tiempo total dedicado a cada soldadura, lo que puede no ser práctico en entornos de producción donde se requiere una alta velocidad de trabajo.
MIG (Metal Inert Gas):
- Menor calidad de soldadura que TIG: Aunque la soldadura MIG es rápida y eficiente, generalmente no produce la misma calidad de soldadura que el proceso TIG. Debido a la velocidad de deposición más alta y la alimentación automática del material de relleno, las soldaduras MIG pueden ser menos limpias y estéticamente atractivas, especialmente en aplicaciones que requieren una apariencia de alta calidad y detalle.
- Más humos y gases: Durante el proceso de soldadura MIG, se generan más humos y gases debido a la combustión del electrodo de metal consumible y la protección del arco con gases inertes o mezclas de gases. Esto puede plantear problemas de seguridad y salud ocupacional en entornos mal ventilados, y requerir medidas adicionales de control de humos y ventilación para garantizar un ambiente de trabajo seguro para los soldadores y otros trabajadores presentes.
Materiales
La selección adecuada de materiales es fundamental en cualquier proceso de soldadura, ya que los electrodos utilizados desempeñan un papel crucial en la calidad, durabilidad y rendimiento de las uniones soldadas.
Tanto en el proceso TIG como en el MIG, la elección del electrodo o material de relleno adecuado depende del tipo de metal a soldar, las propiedades requeridas de la unión soldada y las condiciones específicas de la aplicación.
En esta sección, exploraremos los materiales más comúnmente utilizados en ambos procesos de soldadura, desde los electrodos de tungsteno en TIG hasta los diferentes tipos de electrodos y materiales de relleno en MIG.
Al comprender las características y aplicaciones de estos materiales, podemos tomar decisiones más informadas y eficaces en el proceso de soldadura.
Electrodo TIG:
- Tungsteno puro (WP): El tungsteno puro es uno de los materiales más comunes utilizados como electrodo en el proceso TIG. Ofrece una excelente estabilidad del arco y resistencia a altas temperaturas, lo que lo hace adecuado para soldar una variedad de metales, incluyendo acero inoxidable, aluminio y cobre.
- Tungsteno con torio (WT20): El tungsteno con torio es una opción popular debido a su mayor capacidad de carga de corriente y su vida útil más larga en comparación con el tungsteno puro. Se utiliza comúnmente en aplicaciones de soldadura de acero al carbono, acero inoxidable y níquel.
- Tungsteno con lantano (WL15): El tungsteno con lantano es otra alternativa al tungsteno puro, conocida por su mejor rendimiento en corriente continua (DC) y corriente alterna (AC). Tiene una menor tasa de desgaste y una mayor resistencia a la contaminación, lo que lo hace adecuado para soldaduras de alta calidad en una variedad de materiales.
- Tungsteno con cerio (WC20): El tungsteno con cerio es preferido por su capacidad para operar en corriente continua (DC) y corriente alterna (AC), así como por su menor sensibilidad a la contaminación. Se utiliza en aplicaciones que requieren una mayor penetración y velocidad de soldadura, como la soldadura de acero inoxidable y aleaciones de níquel.
Electrodo MIG:
- Acero: Los electrodos MIG para soldadura de acero están disponibles en una variedad de composiciones, incluyendo acero al carbono y acero inoxidable. Estos electrodos están diseñados para proporcionar un depósito de soldadura fuerte y duradero en una amplia gama de aplicaciones industriales y de fabricación.
- Aluminio: Los electrodos MIG para soldadura de aluminio están específicamente formulados para soldar este metal ligero y altamente conductor. La composición del electrodo se adapta para garantizar una fusión adecuada del aluminio y una soldadura de alta calidad con una buena resistencia y apariencia.
- Acero inoxidable: Los electrodos MIG para soldadura de acero inoxidable están diseñados para proporcionar una unión fuerte y resistente a la corrosión en aplicaciones donde se requiere una alta resistencia a la oxidación y la corrosión. Estos electrodos están disponibles en diferentes grados de acero inoxidable para adaptarse a diversas aplicaciones industriales.
- Magnesio: Los electrodos MIG para soldadura de magnesio están formulados para unir este metal ligero y resistente. Se utilizan en aplicaciones donde se requiere una alta resistencia y durabilidad, como la fabricación de componentes de automóviles y aeronaves.
la selección cuidadosa de materiales es esencial para garantizar el éxito en cualquier proceso de soldadura, ya sea TIG o MIG.
Desde los electrodos de tungsteno en TIG hasta los diversos tipos de electrodos y materiales de relleno en MIG, cada material tiene sus propias características y aplicaciones específicas.
Es crucial considerar factores como el tipo de metal a soldar, las propiedades requeridas de la unión soldada y las condiciones de la aplicación para elegir el material más adecuado.
Al comprender las ventajas y desventajas de cada opción, los soldadores pueden tomar decisiones informadas que contribuyan a la calidad, durabilidad y rendimiento de las soldaduras.
Con una selección adecuada de materiales, se puede lograr una soldadura eficaz y de alta calidad en una amplia gama de aplicaciones industriales y de fabricación.
Preparación
La preparación adecuada es fundamental en cualquier proceso de soldadura para garantizar la calidad y durabilidad de las uniones soldadas.
En esta sección, exploraremos los diferentes requisitos de preparación para los electrodos utilizados en los procesos de soldadura TIG y MIG.
Cada proceso tiene sus propias necesidades específicas de preparación, que afectan directamente el rendimiento y la eficacia de la soldadura.
Electrodo TIG:
Para el proceso TIG, una parte crucial de la preparación implica el afilado del extremo del electrodo de tungsteno.
Este proceso implica dar forma al extremo del electrodo en un punto agudo o un ángulo específico, lo que ayuda a mantener un arco eléctrico estable y concentrado durante la soldadura.
El afilado del electrodo es esencial para garantizar una soldadura de alta calidad y reducir la posibilidad de contaminación del baño de soldadura.
Electrodo MIG:
En contraste, el proceso MIG no requiere preparación específica del electrodo antes de la soldadura. Los electrodos utilizados en MIG están diseñados para alimentarse automáticamente a través del equipo de soldadura, lo que elimina la necesidad de afilar o preparar manualmente el electrodo antes de su uso.
Esto simplifica el proceso y hace que la soldadura MIG sea más fácil y rápida de ejecutar en comparación con otros métodos.
Conclusión:
La preparación adecuada del electrodo es esencial para garantizar la calidad y la eficacia en el proceso de soldadura. Mientras que en el proceso TIG se requiere el afilado del electrodo de tungsteno para mantener un arco estable, en el proceso MIG no se necesita preparación previa del electrodo.
Al entender y seguir los procedimientos de preparación adecuados para cada proceso, los soldadores pueden lograr soldaduras de alta calidad y duraderas en una variedad de aplicaciones industriales y de fabricación.
Corriente
En el proceso de soldadura, la corriente juega un papel crucial en el rendimiento y la calidad de la soldadura. Veamos cómo se aplica la corriente en los electrodos utilizados en los procesos TIG y MIG:
Electrodo TIG:
En el proceso TIG, se puede utilizar tanto corriente continua (CC) como corriente alterna (CA), dependiendo de la aplicación y el tipo de material que se esté soldando.
- Corriente continua (CC): En la soldadura TIG con corriente continua, la corriente fluye en una sola dirección, ya sea desde el electrodo de tungsteno hacia el material base (polaridad directa) o desde el material base hacia el electrodo (polaridad inversa). La corriente continua es adecuada para soldar una variedad de metales, incluyendo acero inoxidable, acero al carbono, níquel y cobre.
- Corriente alterna (CA): En la soldadura TIG con corriente alterna, la dirección de la corriente se invierte periódicamente entre el electrodo y el material base. Esto ayuda a romper la capa de óxido en la superficie del metal base, mejorando la penetración y facilitando la soldadura de materiales como aluminio y magnesio. La corriente alterna es especialmente útil para evitar la formación de inclusiones de óxido en la soldadura de aluminio.
Electrodo MIG:
En el proceso MIG, generalmente se utiliza corriente continua (CC) para la soldadura. La corriente continua fluye de manera constante desde el electrodo consumible hacia el material base, lo que proporciona la energía necesaria para fundir el electrodo y depositar el material de relleno en la unión soldada.
- Corriente continua (CC): La soldadura MIG con corriente continua es ampliamente utilizada en una variedad de aplicaciones industriales. Proporciona un control preciso sobre la velocidad de deposición del material de relleno y la penetración en el metal base, lo que permite soldaduras consistentes y de alta calidad en una amplia gama de materiales, incluyendo acero al carbono, acero inoxidable y aluminio.
Tanto en el proceso TIG como en el MIG, la selección de la corriente adecuada es crucial para lograr soldaduras de alta calidad y durabilidad.
Ya sea corriente continua (CC) o corriente alterna (CA), cada método tiene sus propias aplicaciones y beneficios específicos, que deben tenerse en cuenta según las necesidades y requisitos de soldadura de cada proyecto.
Idoneidad
El proceso de soldadura TIG y MIG ofrece distintas ventajas y aplicaciones, lo que los hace ideales para diferentes tipos de trabajos y contextos industriales:
Electrodo TIG:
Este proceso es ideal para trabajos que requieren precisión y alta calidad. El control preciso del arco y la habilidad para trabajar con una variedad de materiales lo hacen ideal para aplicaciones donde la estética y la precisión son fundamentales. TIG es ampliamente utilizado en industrias como la aeroespacial, la automotriz, la electrónica y la fabricación de equipos médicos.
Electrodo MIG:
Por otro lado, la soldadura MIG es ideal para trabajos que priorizan la producción y la velocidad. La alimentación automática del electrodo y el material de relleno permite una soldadura rápida y eficiente, lo que la hace perfecta para la fabricación en serie y la construcción de estructuras metálicas. MIG se encuentra comúnmente en la fabricación de automóviles, la industria de la construcción y la fabricación general.
Mientras que TIG es preferido en trabajos que requieren alta precisión y calidad, MIG es la elección ideal cuando la eficiencia y la velocidad son prioridades principales.
La selección entre los dos procesos de soldadura depende de las necesidades específicas del proyecto, el tipo de material y los requisitos de calidad del producto final.
Conclusiones sobre las diferencias entre las máquinas de soldar TIG y MIG
En conclusión, las máquinas de soldar TIG y MIG presentan diferencias significativas en términos de técnica, aplicaciones y resultados finales:
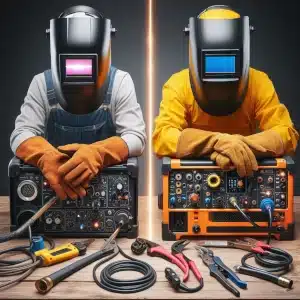
- Técnica y habilidades requeridas:
- TIG requiere un mayor nivel de habilidad y destreza por parte del soldador debido a la necesidad de controlar simultáneamente la alimentación del electrodo, la velocidad de avance y el flujo de gas, mientras se mantiene el arco. Por otro lado, MIG es más fácil de aprender y usar, ya que la alimentación del electrodo y el flujo de gas son controlados automáticamente por la máquina.
- Calidad del cordón de soldadura:
- TIG produce cordones de soldadura limpios y de alta calidad, con menos salpicaduras y escoria, lo que lo hace ideal para aplicaciones donde se requiere una apariencia estética y una soldadura de alta calidad. MIG, aunque puede producir cordones de soldadura fuertes y eficientes, tiende a tener más salpicaduras y puede dejar una pequeña cantidad de escoria, haciéndolo menos adecuado para aplicaciones que requieren un acabado estético de alta calidad.
- Material de relleno y preparación:
- En TIG, el material de relleno se agrega manualmente mediante una varilla o alambre de aporte separado, mientras que en MIG, el aporte de material se realiza a través del electrodo tubular, lo que simplifica el proceso. Además, TIG requiere la preparación del electrodo de tungsteno mediante el afilado del extremo, mientras que MIG no requiere preparación previa del electrodo.
- Corriente utilizada:
- TIG puede operar con corriente continua (CC) o corriente alterna (CA), lo que lo hace versátil para diferentes tipos de materiales y aplicaciones. MIG, por otro lado, utiliza corriente continua (CC).
- Aplicaciones:
- TIG es adecuado para una amplia gama de materiales y es ideal para trabajos que requieren precisión y alta calidad, como la industria aeroespacial, la fabricación de equipos médicos y la joyería. Mientras tanto, MIG es más adecuado para trabajos de producción y mayor velocidad, como la fabricación de automóviles, la construcción de estructuras metálicas y la fabricación general.
En resumen, la elección entre TIG y MIG depende de los requisitos específicos del proyecto, incluyendo el tipo de material, la calidad deseada de la soldadura, la velocidad de producción y las habilidades del operador.
Cada proceso tiene sus propias ventajas y desventajas, y es importante seleccionar el método de soldadura más adecuado para cada situación.
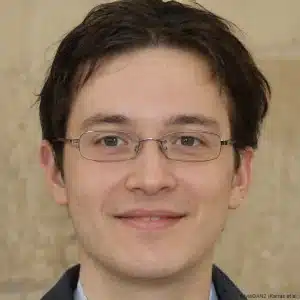
Con más de 25 años de experiencia en el sector de las ventas de equipamiento para el hogar, herramientas de bricolaje, y en los últimos 15 años en una empresa de reformas de albañilería, venta de azulejos y materiales de construcción, estufas leña, pellets, chimeneas, sistemas de calefacción.
Máster Técnico Superior en riesgos laborales.
Licenciado por la Universidad de Alicante ua.es