En este artículo, exploraremos los problemas de un soldador inverter MMA más comunes y proporcionaremos soluciones prácticas para abordar cada uno de ellos.
Desde dificultades para encender el arco hasta sobrecalentamiento y interferencias en la corriente de soldadura, analizaremos las posibles causas subyacentes de estos problemas y ofreceremos consejos sobre cómo diagnosticar y resolver eficazmente cada situación.
Ya sea que seas un soldador profesional o un entusiasta del bricolaje, comprender los problemas potenciales de un soldador inverter MMA y saber cómo solucionarlos te ayudará a mantener tu equipo en óptimas condiciones, garantizando soldaduras seguras y de alta calidad en cualquier situación.
Los soldadores inverter MMA (Metal Manual Arc) son ampliamente utilizados en la industria y en aplicaciones domésticas debido a su portabilidad y eficiencia.
Sin embargo, como cualquier equipo, pueden presentar problemas. Aquí tienes algunos problemas comunes que podrían surgir con un soldador inverter MMA y posibles soluciones:
Tabla de Contenidos
Falta de arco o dificultad para encender el arco
Cuando experimentas una falta de arco o dificultad para encender el arco al soldar con un soldador inverter MMA, puede ser frustrante y detener el progreso del trabajo.
Aquí hay una descripción más detallada de los posibles factores que podrían estar contribuyendo a este problema, así como las soluciones correspondientes:
- Mala conexión del electrodo: La conexión del electrodo al portaelectrodos puede ser deficiente debido a la presencia de suciedad, óxido o residuos de soldadura en el área de contacto. Esto puede resultar en una mala transferencia de corriente al electrodo, lo que dificulta o impide la creación de un arco estable.
- Solución: Verifica que la conexión del electrodo esté limpia y libre de cualquier suciedad o residuo. Limpia tanto el portaelectrodos como el extremo del electrodo con un cepillo de alambre o una herramienta adecuada para eliminar cualquier contaminante. Asegúrate de que el electrodo esté firmemente sujeto en el portaelectrodos para garantizar una buena transferencia de corriente.
- Configuración incorrecta de la corriente de soldadura: La corriente de soldadura debe ajustarse de acuerdo con el diámetro y el tipo de electrodo utilizado, así como el tipo y el grosor del metal base. Una corriente demasiado baja puede no ser suficiente para encender el arco, mientras que una corriente demasiado alta puede hacer que el electrodo se funda rápidamente sin formar un arco estable.
- Solución: Verifica la configuración de la corriente de soldadura en tu soldador inverter y ajústala según las recomendaciones del fabricante del electrodo y las especificaciones del trabajo de soldadura. Utiliza una corriente adecuada para el diámetro del electrodo y el grosor del metal base para garantizar una operación óptima.
- Mala tierra: Una conexión deficiente entre la pinza de tierra y el metal base puede interferir con la circulación de corriente necesaria para crear un arco estable. Esto puede deberse a la presencia de óxido, pintura u otros recubrimientos en la superficie de trabajo.
- Solución: Verifica que la pinza de tierra esté conectada firmemente a una superficie metálica limpia y libre de recubrimientos. Si es necesario, raspa o lija la superficie de trabajo para eliminar cualquier recubrimiento que pueda interferir con la conexión eléctrica. Asegúrate de que la pinza de tierra esté colocada lo más cerca posible del área de soldadura para minimizar la resistencia eléctrica.
Al abordar estos posibles problemas y aplicar las soluciones correspondientes, deberías poder superar la falta de arco o la dificultad para encender el arco al soldar con un soldador inverter MMA.
Sin embargo, si el problema persiste, es recomendable buscar asistencia adicional de un técnico calificado o del fabricante del equipo.
Electrodos que se pegan o se funden
Cuando los electrodos se pegan al material base o se funden demasiado rápido durante el proceso de soldadura, es importante identificar y corregir el problema para garantizar una soldadura de calidad.
Aquí se detallan las posibles causas y soluciones:
- Corriente de soldadura demasiado alta: Si la corriente de soldadura es demasiado alta para el electrodo y el material base que estás utilizando, los electrodos se fundirán rápidamente y podrían pegarse al metal base.
- Solución: Reducir la corriente de soldadura en el soldador inverter. Consulta las especificaciones del electrodo y del material base para determinar la configuración óptima de corriente.
- Técnica de soldadura incorrecta: Una técnica de soldadura inadecuada, como mantener el electrodo en un solo lugar durante demasiado tiempo o moverlo demasiado rápido, puede provocar que los electrodos se peguen o se fundan rápidamente.
- Solución: Ajusta tu técnica de soldadura. Mantén un arco estable entre el electrodo y el material base, y muévete a un ritmo constante para evitar que el electrodo se caliente demasiado y se pegue al metal base. Practica diferentes técnicas de movimiento del electrodo para encontrar la más adecuada para el trabajo en cuestión.
- Tipo incorrecto de electrodo: Si estás utilizando un electrodo que no es adecuado para el tipo de material base o la aplicación específica, es posible que experimentes problemas como electrodos que se pegan o se funden demasiado rápido.
- Solución: Asegúrate de seleccionar el tipo correcto de electrodo para el material base y la aplicación. Consulta las recomendaciones del fabricante del electrodo y del soldador inverter para garantizar una selección adecuada.
Al implementar estas soluciones, puedes evitar que los electrodos se peguen o se fundan demasiado rápido durante el proceso de soldadura, lo que te permitirá lograr soldaduras más limpias y de mayor calidad.
Además, siempre es recomendable practicar y familiarizarse con diferentes configuraciones y técnicas de soldadura para mejorar tus habilidades como soldador.
Sobrecalentamiento o cortocircuito
Cuando un soldador inverter experimenta sobrecalentamiento o cortocircuitos frecuentes, es crucial abordar el problema de manera adecuada para evitar daños mayores en el equipo y garantizar un funcionamiento seguro.
A continuación, se describen las posibles causas y soluciones:
- Obstrucciones en el sistema de enfriamiento: Las obstrucciones en los ventiladores de enfriamiento o en las rejillas de ventilación pueden dificultar el flujo de aire necesario para disipar el calor generado durante la soldadura, lo que resulta en un sobrecalentamiento del soldador.
- Solución: Apaga el soldador inverter inmediatamente y déjalo enfriar por completo. Luego, inspecciona los ventiladores de enfriamiento y las rejillas de ventilación para asegurarte de que no haya acumulación de suciedad, polvo u otros obstáculos. Limpia cualquier obstrucción con cuidado utilizando aire comprimido, un cepillo suave o un paño seco.
- Entorno de trabajo inadecuado: Si el soldador inverter se utiliza en un entorno con poca ventilación o en condiciones extremadamente calurosas, puede resultar en un sobrecalentamiento del equipo.
- Solución: Verifica que el área alrededor del soldador esté bien ventilada para permitir un flujo de aire adecuado. Si es posible, coloca el soldador en un lugar con temperaturas ambiente moderadas y evita trabajar bajo la luz directa del sol. Considera utilizar ventiladores adicionales o sistemas de refrigeración portátiles si es necesario.
- Problemas internos del equipo: Los cortocircuitos frecuentes pueden indicar problemas internos en el soldador inverter, como componentes eléctricos defectuosos o fallos en el sistema de protección contra sobrecargas.
- Solución: Si el problema persiste después de verificar y limpiar el sistema de enfriamiento y garantizar un entorno de trabajo adecuado, es probable que el soldador inverter necesite ser reparado por un técnico especializado. Evita intentar reparar el equipo por tu cuenta, ya que esto podría provocar daños adicionales o lesiones personales.
Al enfrentarse a problemas de sobrecalentamiento o cortocircuitos en un soldador inverter, es importante tomar medidas inmediatas para prevenir daños mayores.
Esto incluye apagar el equipo, permitir que se enfríe adecuadamente, verificar y limpiar el sistema de enfriamiento, garantizar un entorno de trabajo bien ventilado y, si es necesario, buscar la asistencia de un técnico calificado para reparaciones adicionales.
Ruido o interferencia en la corriente de soldadura
Cuando experimentas ruido o interferencia en la corriente de soldadura al usar un soldador inverter, es fundamental identificar y abordar la causa del problema para mantener un proceso de soldadura efectivo y seguro.
Aquí se detallan las posibles causas y soluciones:
- Problemas eléctricos en el equipo:
- Cables sueltos o dañados: Los cables de alimentación o los cables internos del soldador pueden estar sueltos o dañados, lo que podría causar interferencia en la corriente de soldadura.
- Conexiones defectuosas: Las conexiones eléctricas internas del soldador inverter podrían no estar bien conectadas, lo que puede resultar en ruido o interferencia en la corriente de soldadura.
- Componentes electrónicos defectuosos: Los componentes internos del soldador, como transformadores o circuitos de control, pueden estar defectuosos, lo que podría causar problemas eléctricos y generar interferencia en la corriente de soldadura.
- Solución: Verifica cuidadosamente todas las conexiones eléctricas del soldador inverter, incluidos los cables de alimentación y las conexiones internas. Asegúrate de que estén bien ajustadas y que no haya cables sueltos o dañados. Si encuentras algún problema, repara o reemplaza los componentes según sea necesario. Si el problema persiste, es posible que necesites llevar el soldador a un técnico especializado para una inspección más detallada y posibles reparaciones.
- Interferencia electromagnética externa:
- Dispositivos eléctricos cercanos: La presencia de dispositivos eléctricos o electrónicos cercanos al soldador inverter puede causar interferencia electromagnética en la corriente de soldadura.
- Fuentes de energía externas: Las fuentes de energía externas, como líneas de alta tensión o equipos industriales, pueden generar campos electromagnéticos que interfieren con la corriente de soldadura.
- Solución: Aleja el soldador inverter de cualquier dispositivo eléctrico que pueda estar causando interferencia electromagnética. Apaga o desconecta temporalmente los dispositivos cercanos durante el proceso de soldadura para minimizar la interferencia. Además, evita soldar cerca de fuentes de energía externas conocidas, si es posible.
Al abordar estos posibles problemas y seguir las soluciones sugeridas, puedes reducir o eliminar el ruido y la interferencia en la corriente de soldadura, lo que te permitirá realizar soldaduras más limpias y de mayor calidad.
Si el problema persiste después de realizar estas acciones, es recomendable buscar la asistencia de un técnico especializado para diagnóstico y reparación adicionales.
Conclusiones sobre los problemas de un soldador inverter MMA
En conclusión, los problemas comunes que pueden surgir con un soldador inverter MMA pueden variar desde dificultades para encender el arco hasta sobrecalentamiento, electrodos que se pegan o interferencias en la corriente de soldadura.
Es crucial identificar y abordar estos problemas de manera oportuna para garantizar un funcionamiento seguro y eficiente del equipo. Algunas conclusiones importantes son:
- Identificación temprana de problemas: Es fundamental reconocer los signos de problemas, como dificultades para encender el arco, electrodos pegados o sobrecalentamiento, para abordarlos de manera rápida y eficaz.
- Diagnóstico adecuado: Cada problema puede tener múltiples causas subyacentes, desde problemas eléctricos internos hasta interferencia electromagnética externa. Un diagnóstico cuidadoso es necesario para determinar la causa raíz del problema.
- Mantenimiento preventivo: Mantener el equipo en buenas condiciones, limpiando regularmente los componentes, verificando las conexiones eléctricas y asegurándose de que el área de trabajo esté bien ventilada puede prevenir muchos problemas antes de que ocurran.
- Soluciones específicas: Cada problema requiere soluciones específicas. Desde ajustar la corriente de soldadura hasta verificar las conexiones eléctricas y alejar el soldador de fuentes de interferencia electromagnética, es importante abordar cada problema de manera adecuada.
- Profesionalismo y seguridad: Si los problemas persisten o no puedes identificar la causa, es fundamental buscar ayuda profesional. Trabajar con un soldador inverter defectuoso puede ser peligroso y puede resultar en lesiones personales o daños al equipo.
En resumen, al enfrentarse a problemas con un soldador inverter MMA, es esencial actuar con prontitud, diagnosticar con precisión y aplicar soluciones específicas para garantizar un funcionamiento seguro y efectivo del equipo.
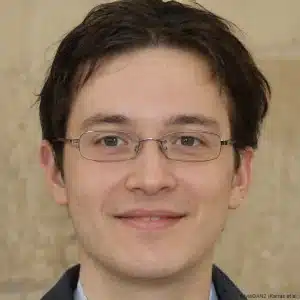
Con más de 25 años de experiencia en el sector de las ventas de equipamiento para el hogar, herramientas de bricolaje, y en los últimos 15 años en una empresa de reformas de albañilería, venta de azulejos y materiales de construcción, estufas leña, pellets, chimeneas, sistemas de calefacción.
Máster Técnico Superior en riesgos laborales.
Licenciado por la Universidad de Alicante ua.es